How to beat the challenges of starting automatic hollow core production?
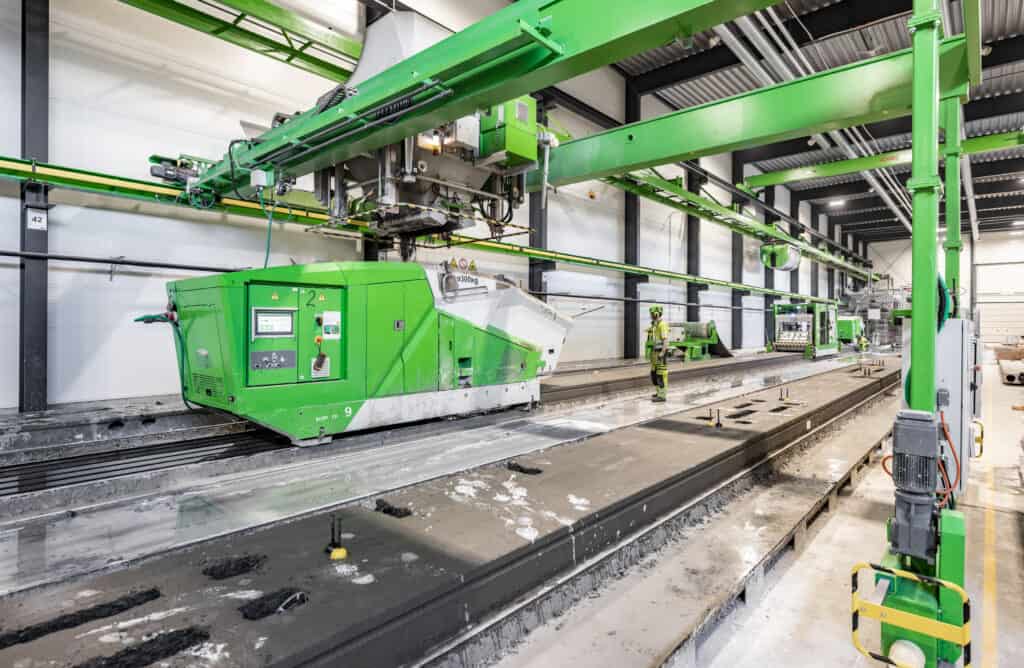
What are the prerequisites for successful transition to automatic machines in hollow-core production? How to ensure the process goes smoothly, and what are the typical pitfalls precast factories face in this change? Continue reading to discover how production can be optimized with automatic machines, and how potential challenges in regard to personnel, data, setting up and running machinery and maintaining machinery can be overcome.
Automation and digitalization breakthrough began in the hollow-core industry already in the 90s, however, the move towards automatic machinery has significantly started only over the past decade. There are also some concerns, though, and over the years we have identified four challenge areas – personnel, data, setting up and running the machine and maintenance of automatic machines – all of which can be overcome.
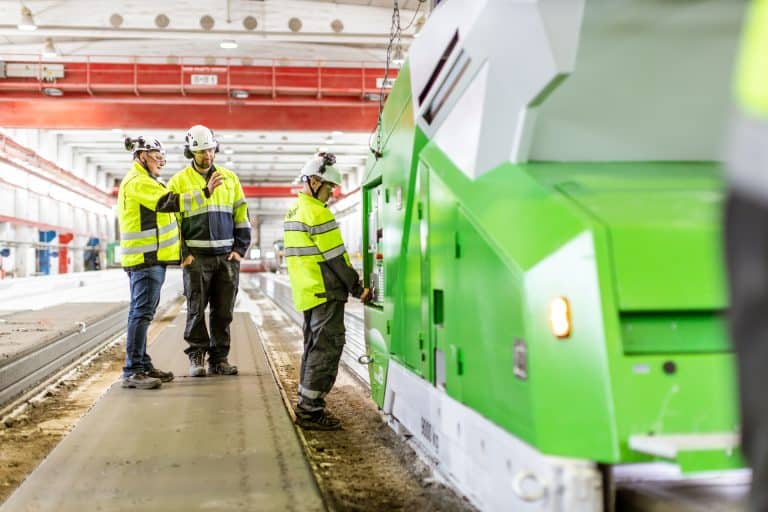
Writer
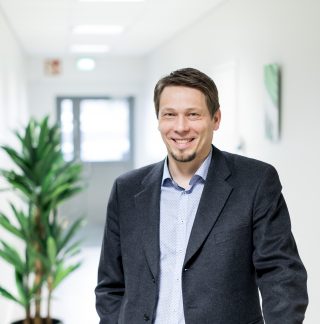
Jani Eilola,
Product Director, Floor Technologies
Elematic
Challenge #1: Personnel and automatic production
Resistance to change is common human behavior and likely to appear among your personnel whenever you are planning or conducting changes to your production. To diminish the impacts of resistance to change, I suggest involving your team to the change projects early on. Involving people allows them to better internalize the benefits that come with the machinery update: healthier and safer working environment, less heavy work and more modern tools; more touch screens and less shovels.
Automation may also be considered a threat – people are afraid of losing their jobs – because the target is to reduce man hours per square meter and improve efficiency. But if you take a look at the matter from another perspective, the use of automated machines has a potential to increase competitiveness which may create more sales and thus lay-offs could be avoided. You can also ask what happens if nothing is done? The visionaries reap the benefits of new technology simply because they can influence the development while others just follow.
When taking automatic machines into use, your team also needs to learn new skills; how to safely operate the machines, how to use the operating system and how to maintain the machines – to charge batteries, check sensors and add ink, for example. Some people may not want to change their ways of working while others are eager to learn and make improvements; in such a case, it’s good to redefine job descriptions to match the interests of different people, if possible.
New factory practices and their effects to the whole process must also be understood – the machines do not have a driver anymore, instead the machines are set-up at the beginning of the bed and send to operate independently. In order for the machines to operate independently, the production planning team needs to learn how to use available workforce efficiently in a new environment, how to use a manufacturing execution system, such as FloorMES, which is needed for operation of automatic machinery, and communicate with engineering to optimize plans for automation. In addition, it is important that the team leaders learn how to lead the team in the changed environment. Detailed daily schedules, produced in FloorMES, can help in organizing and following-up the daily workflow.
Training your people is the key to success in adapting automatic machinery. In that we can help you by providing training when new machines are delivered to your factory, whenever needed or through service contract visits. Furthermore, it is essential to continue training whenever new employees are hired.
Challenge #2: Data and automatic production
Data is a big issue in the context of automatic machines – the machines need correct data to work, they cannot read minds. As an example, if you have an opening of 200 mm x 400 mm, the machine also needs to know the depth of the opening if it is a through hole or a recess of a certain depth. For this to happen, you need to establish rules for engineering the slabs, for example, how all the markings and openings are marked within your company and together with your outsourced partners. Our philosophy is that the machines will follow the design 1:1, which means that you can always follow-up on what the machines are doing. Of course, exceptions are sometimes needed but they should be used as the last resort. In my opinion, the rule of thumb is to always have designs the machines can precisely follow.
Furthermore, the data needs to be compatible between design and production software. Building a software architecture where all parts work together seamlessly is not an easy task and definitely a time and resource consuming one. Hence, we have designed Elematic Plant Control ERP and its manufacturing execution modules, the FloorMES, to provide seamless data flow between designers that use, for example, Tekla Structures, the precast plants and the automatic machines.
Of course, automatic machines need different kind of support than regular precast machines. For the purpose, we established a software unit. A specialized team provides quick and continuous support and at the same time gathers information for developing the software and machines further. With the collected data and knowledge, future IoT (Internet of Things) solutions can be implemented effectively. Our aim is to help you to stay on top of the construction evolution.
Challenge #3: Setting up and running automatic machines
In the setting up stage automatic machines come with special needs; however, these tend to be minor issues and can usually be easily solved. In automatic machines, laser positioning is always in use, and thus, there needs to be a place for a reflector mirror. The mirror should be positioned so that the laser can see over or around the machine, either forward or backward. The laser stands are always tailored on case-by-case basis.
Another thing to bear in mind is the straightness of the rails, because it affects the laser. If you have a slight curve on the rails, the laser will move on the mirror as the machine moves. In such a case you might need to install a bigger mirror or have two smaller ones in place. In addition, the rail gauge should be checked; the accuracy of automatic machines is affected by a slack on wheels. I recommend checking these issues before making a purchase decision for an automatic machine.
Cleanness of the rails is also important, because automatic machines have to be able to position themselves accurately. For example, some particles under the wheels may result in slight movement of the machine, which again impacts the accuracy. Concrete deposit may cause interruptions, and thus, it is important to have clean working environment for the automatic machines.
Challenge #4: Maintenance of automatic machines
Maintaining automatic machines differs slightly from the maintenance of regular machines. Some special maintenance tasks include correctly adjusting the sensors to avoid tripping and cleaning lights sensors and mirrors. In general, automatic machines should be handled with care because of the added wiring, sensors and other vulnerable components.
In order to conduct new maintenance tasks, the maintenance team needs to expand their skillset. For example, electrical and automation service people need to learn how to change the sensors and adjust parameters. Of course, they may also need new tools for doing the tasks, such as a laptop for adjusting parameters. The maintenance is something you can do within your factory or outsource the tasks to an external party. Do not worry, we will help you with training and take care of the more complex service tasks, for example, updating software and upgrading components, as we have done before.
Working together is essential from the initial interest in automatic machines to having them in operation. Cooperation is important not only within your company and with your people, but also together with the machine supplier. All of the pitfalls mentioned in this blog are solvable by planning ahead, involving people and transforming factory practices to support production automation. If automatic machines are something that interest you, this article “How can a precast concrete factory prepare for the digital future?” could be worth reading. It sheds more light on steps to be taken prior to considering a purchase for an automatic machine. Remember, going from manual work to automatic production is a big change, but we are here to help you all the way, from initial interest to machine maintenance.