Machine safety risk assessment is an iterative process
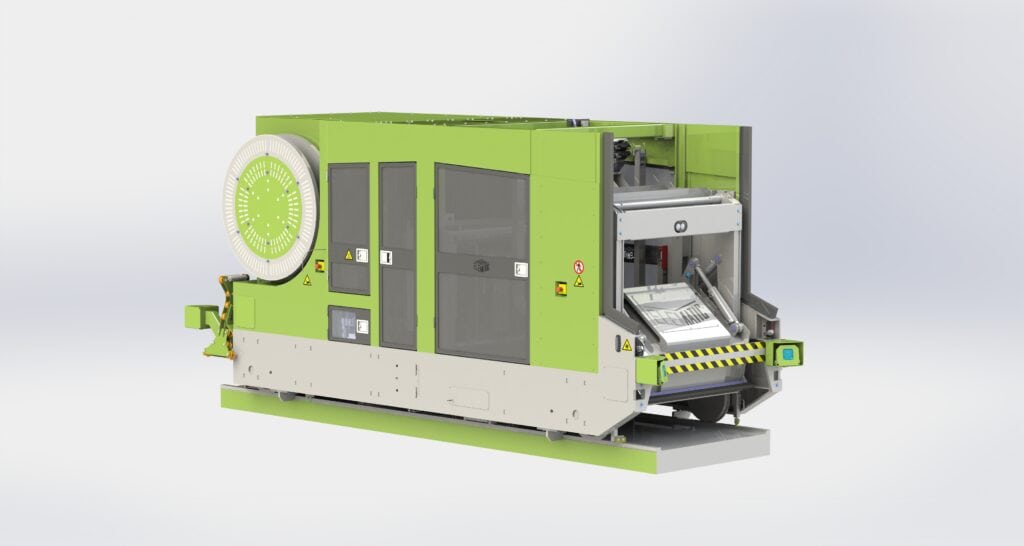
Enabling sustainable and safe building construction is the core of our business. Machine safety is an essential part of it. Let’s look at what improvements have been made recently.
Machine safety improvement and development is a continuous project. Rosa Kritz, Machinery Safety Specialist & Project Manager, R&D, at Elematic, says that identifying and communicating about residual risks has been one of the focus areas recently.
“In risk assessment and risk mitigation the first thing is to eliminate the risk by inherent safe design measures. If the risk can’t be minimized enough with those measures, the next step is to reduce risks by safeguarding measures, for instance adding safety equipment such as safety radar sensors on the moving machine,” Kritz explains. “Sensors recognize a human being and the machine stops. In theory, despite the safety solutions, a tiny risk remains caused by human error, neglect or failure. These types of risks we can’t eliminate but we can warn about them with clear, improved manuals, safety instructions, safety trainings for personnel and adding warning labels on the machines.”
The risk assessment is a long process, and they are done regularly.
“Risk assessment is done every time anything changes in the machine. It is an iterative process which is done in the beginning of a design process and during the design, and whenever there are updates to the machine.”
More visible improvements are that the safety buffers have been changed to safety radars. The latest technology in radars is contactless sensors which tolerate well steam and dirt of the precast factory environment. “We make the risk assessment and, if risks can’t be eliminated or reduced with inherently safe design measures, or the access to the operating area can’t be prevented with other solutions such as safety fences, one option is to add safety radars to monitor the area.” Rosa Kritz adds that new safety radars are not as sensitive to damage as mechanic buffers, and they require less maintenance than buffers. It is also possible to update the old buffers to new radars. LED warning lights are lit when the machine is moving.
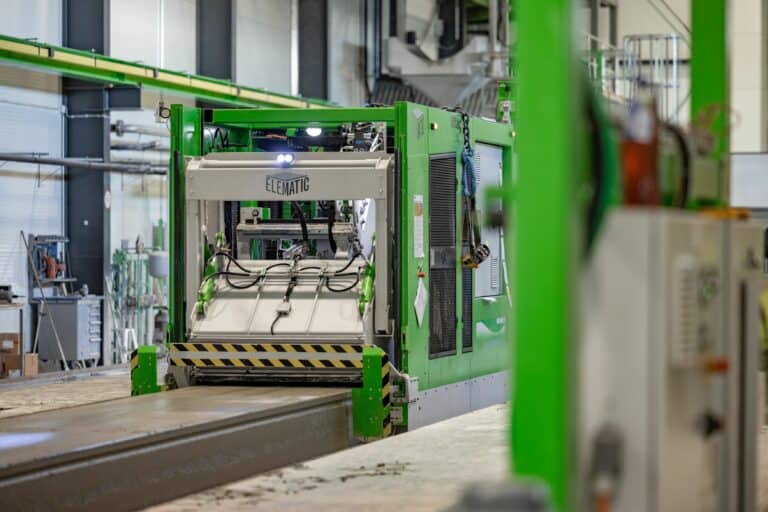
Modifier E9
- Safety radars on both ends stop the machine if they detect human beings.
- Safety edge sensors on the container end stop the movement if there’s any contact on the edges.
- Warning lights flash when the machine is moving.
- Ultrasonic sensors pause operation when there’s an obstacle and prevent collision with the machine moving in the front.
- Doors are linked to operation: if you open a door to reach some machine parts for instance for operation stops before the door opens.
“The Modifier also has the possibility to work with the Extruder and therefore the Modifier has speed control, a warning sound and safety edge sensors. If the sensors detect something that is about to be compressed, they stop the movement. This is because the extruder and modifier run sequentially. They work automatically in cooperation, and the modifier inserts the excavated concrete back into the extruder. The Modifier and Extruder together have an automatic recycling function and it has a distance control of the machines so that they do not collide with each other.”
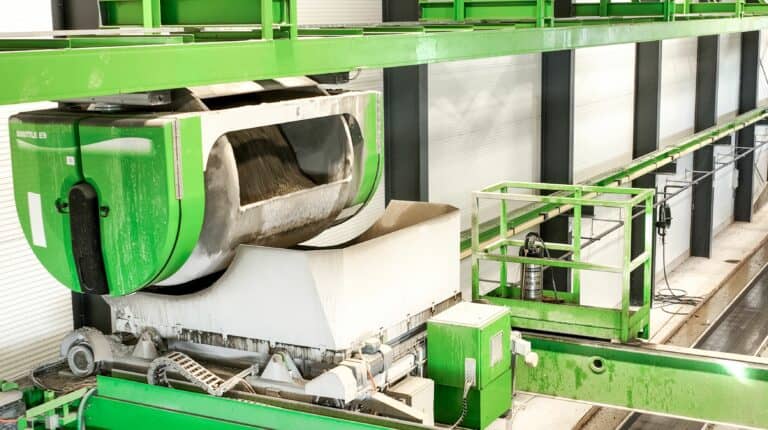
Concrete transportation
“The shuttle transports concrete and moves automatically. It must move high enough that a person can’t reach to touch it. It is prohibited to stay in the area under the shuttle and concrete transportation tracks. Their places of maintenance and washing must be protected and there needs to be sufficient safety measures to prevent the shuttle movement during maintenance.”

Wall lines & shuttering robot
“Both wall and hollow core lines have automatic machines, but wall lines have more automated operating areas which can be protected with fences. This is rarely possible in hollow core production. Also, in wall lines there may be both manual and automatic machines and it is important to consider the process as a whole in safety matters and risks.
For example, the automatic shuttering robot is operating on isolated, fenced area and access to the area is denied when the robot is running. Casting table is moved through a hole in the fence and when the operator secures the area as empty, the safety door is locked and the light curtains in the fence holes are activated.”
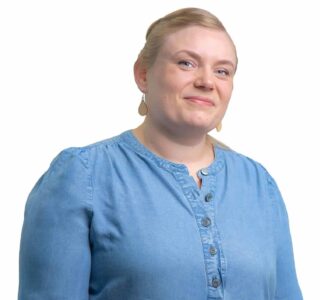
Rosa Kritz, Machinery Safety Specialist & Project Manager, R&D, at Elematic
Want to know more? Please contact us!
or