Recordable incidents down almost 80%
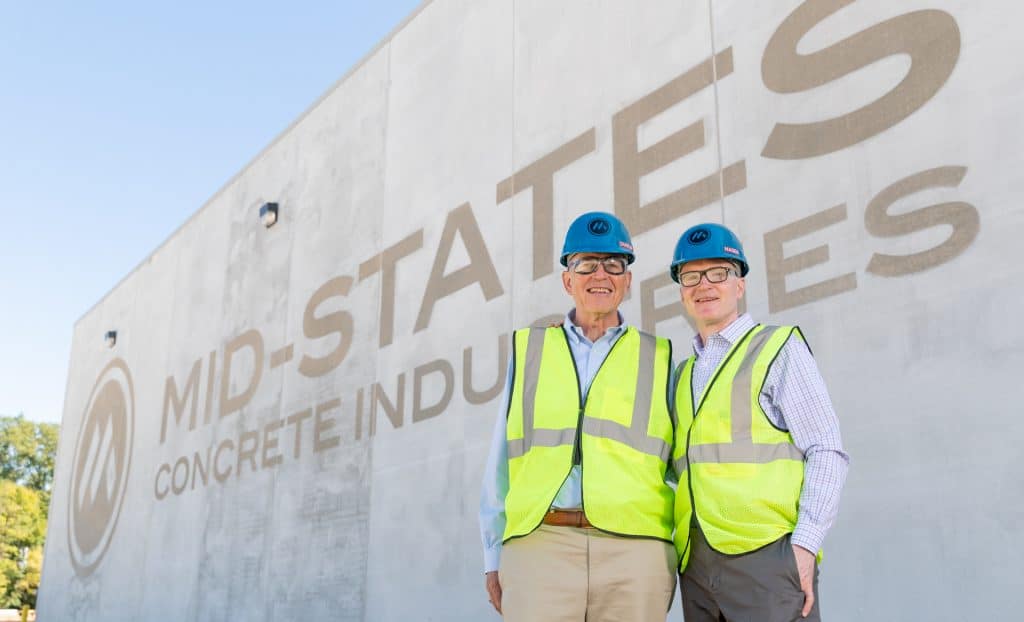
In 2017, Mid-States Concrete Industries was recognized as one of the safest companies in the USA and awarded SHARP designation by the United States Department of Labor Occupational Safety and Health Administration (OSHA). How did they succeed?
Exceptional attitude towards occupational safety is one of the cornerstones of Mid-States’ great story and the SHARP award is a deserved designation of all the efforts the company took over the years. Mid-States joined OSHA’s voluntary On-site Consultation Program in 2010. Since joining the Program, OSHA recordable incidents have dropped by about 80 percent at Mid-States. Plus, the company has seen a significant reduction in its workers’ compensation incidents.
In addition to obligatory safety rules, that all companies in the USA are required to follow and are the subject of regular inspections by OSHA, there are a few voluntary programs available. One of them is Safety & Health Achievement Recognition Program, SHARP.
“The SHARP award is a big deal and part of the reason why we have received it is the help of Elematic. The automation and the safety features of the equipment have helped to keep the workplace safe and keep our employees from getting injuries,” says Mike Wolff, Vice President of Safety and Plant Operations of Mid-States Concrete Industries.
Dust and water regulations are getting stricter
In 2017 the standard for construction regarding respirable silica dust was significantly tightened in the USA. The OSHA rule reduces the exposure limit to 0,05 mg/m3 for all industries. That standard is much more stringent than the previous level of 0,25 mg/m3 for construction and 0,1 mg/m3 for other industries.
Saw cutting of concrete slabs is a daily routine in the precast manufacturing process. Cutting operation releases a crystalline silica in a respirable form. Crystalline silica a common mineral found in many naturally occurring and man-made materials used at construction sites, for example in concrete.
Respirable crystalline silica contains very small particles typically at least 100 times smaller than ordinary sand. This substance is extremely dangerous and can cause lung cancer, silicosis and other respiratory illnesses.
Mid-States was well prepared for this dust regulation change already two years ago when they bought a concrete saw E9-500 from Elematic. Acquisition of the E9-500 saw was part of the bigger modernisation program that was going on at Mid-States. Recently, the company has installed a complete water recycling system in the factory. Most of such measures are dictated by regulations, however, Mid-States thinks ahead and wants to make the necessary changes well in advance.
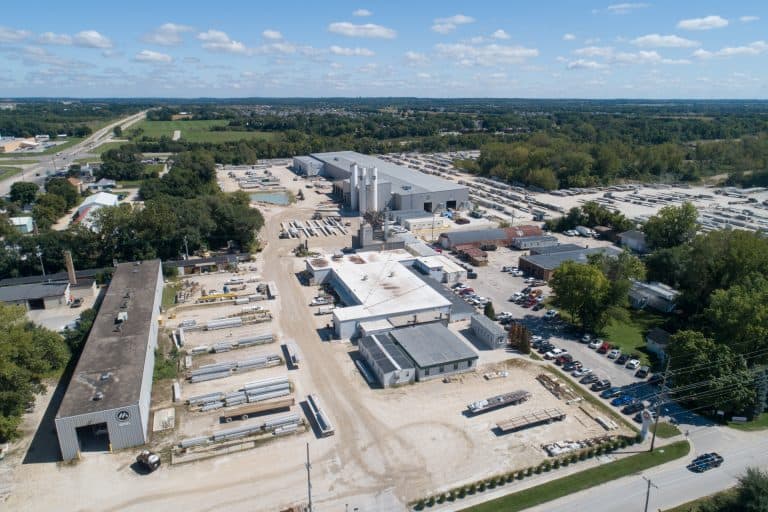
Technology innovation is a driving force
“The adjustable extruder was another innovative system that Elematic has helped us with. Now all the US precasters want to come and see it,” says Wolff. The adjustable extruder is a modified version of the E9 series extruder. A filler machine, as they call it at Mid-States, enables casting of two hollow core slabs of different width on the same bed simultaneously. The narrow slabs of non-standard widths can now be made without longitudinal saw cutting.
There is a market in place and demand for narrow hollow core slabs in the US. This, in turn, is a legacy of an old hollow core manufacturing method called Flexicore, which produced 24” (60 cm) wide slabs. The narrow Flexicore slabs were used for residential housing and the American precast erectors used to have them ready made on the construction site.
After the hollow core manufacturing shifted towards extruding methods, nobody had an idea how to extrude narrow planks. Precasters began to saw standard slabs until Mid-States took the risk and tried to develop a new solution together with Elematic, which resulted in the adjustable extruder.
“We are 100 % satisfied with this adjustable extruder. Mid-States is the first American producer who is using this type of a machine, “emphasizes Wolff.
Currently, Mid-States is also the only one in the US, who has totally replaced all the old standard extruders with the new Elematic E9 extruders
“We are very pleased with their advanced safety and automation features.”
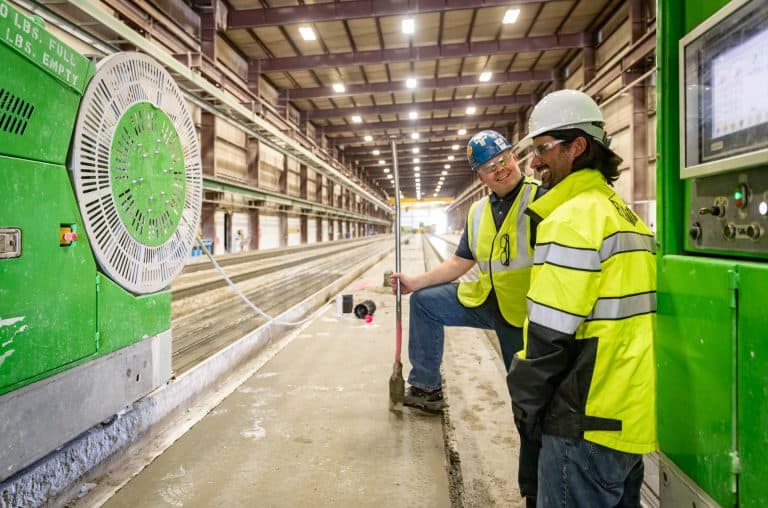
Automate, automate, automate
The rapid development of technology and digitalization have created conditions of a constant change. Climate change, economic change, market change, consumer behaviour change – you name it. The labour pool in the US is also totally changing as it happens all over the world.
For the precast industry, the change means troubles with skilled manpower. For example, right now, Mid-States would need almost 30 employees, but they are nowhere to be found. Hagen Harker, the owner and CEO of the company advises: “to automate, automate, automate”. Automated processes can help the industry to be more attractive to the new generation.
In addition to clean and attractive working environment for the employees, automation means also higher production efficiency and safety. Reduction of the manpower on the production line minimizes risks of injuries. Mid-States takes care of the workers and has a proven low turnover of the employees.
ORDER OUR NEWSLETTER OR CONTACT US!
or