Why use hollow core slabs?
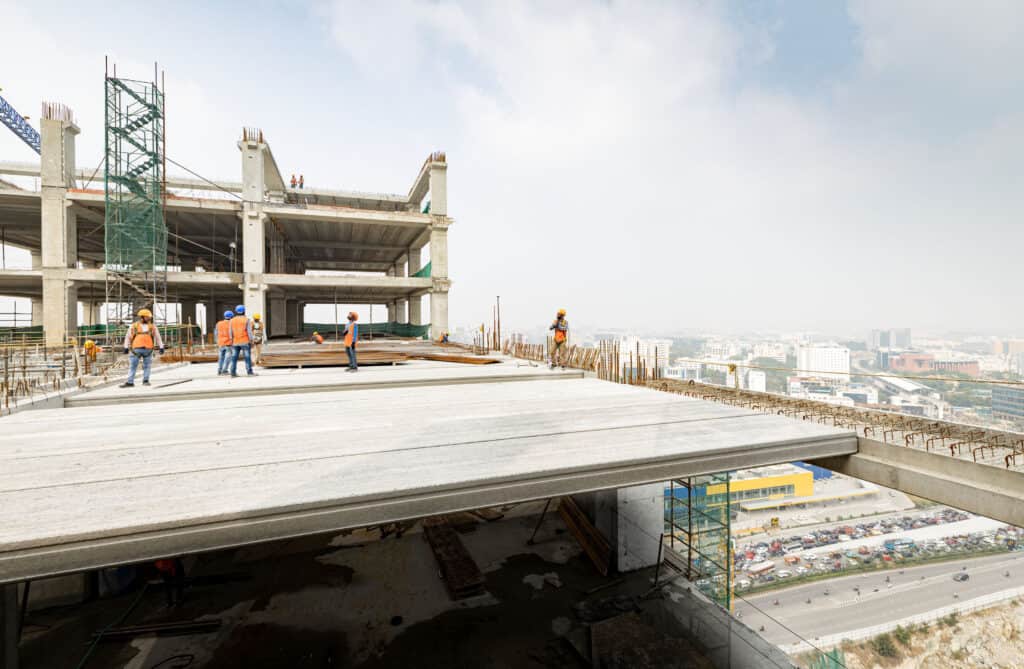
Why use hollow core slabs? These pre-stressed floor slabs with either round or shaped voids are one of the most popular, efficient and long span floor construction components that exist today. Due to long spans, less load-bearing structures such as columns and inner walls are needed. This results in increased architectural and structural freedom and less raw materials used in a building. Continue reading to discover how to benefit from using precast hollow-core slabs.
Versatile product for many purposes
Hollow core slabs are typically used in the construction of floors in multi-storey buildings, in both simple and complex designs of residential, commercial, educational, healthcare and industrial buildings, because of their versatility in spanning capabilities. The thickness of hollow core slabs can vary between 120 – 500 mm and the typical span is 5 – 20 m. They are 1.2 m wide as standard, but other sizes are also sometimes used, e.g. 2.4 m.
The slabs have an excellent fire resistance, high durability and reduced self-weight, which enables meeting earthquake-resistance standards. In addition, their great thermal properties help reducing energy consumption for heating and cooling of buildings. For example, one can utilize hollow core slabs for the construction of unique construction projects, where efficient acoustic properties (up to R’w ≥ 55 dB with standard hollow-core slab solutions) and high load-bearing capabilities are a must. The slabs are also well-suited for affordable housing, where resource-efficient construction is the key.
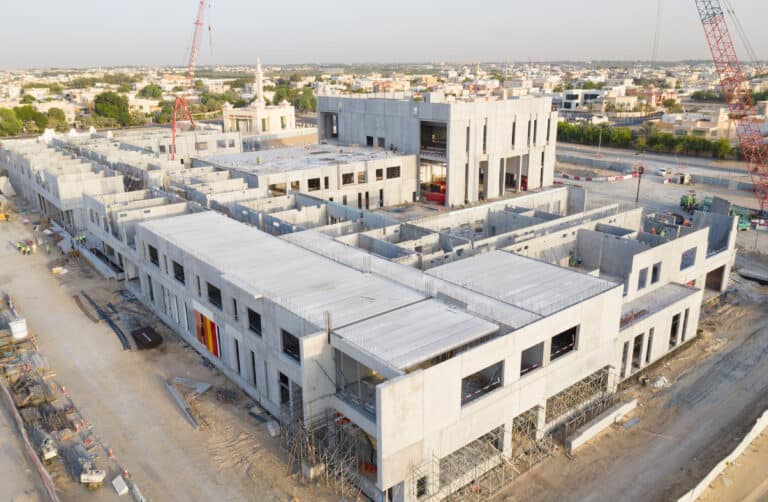
What are hollow core slabs made of?
One fascinating perspective to hollow core slabs is not often discussed. The slabs are made of two materials, the properties of which are taken almost to the extreme. Firstly, concrete: general wet cast concrete strength is C20 / 25, while hollow-core concrete strength is C40 / 50-C50 / 60. That is, more than twice as strong. Of course, special concrete with strength of 100-200 MPa, has been produced for specific purposes but now we are talking about basic construction.
Moreover, prestressing strands are of extremely strong steel. It is often thought that titanium or carbon fiber are stronger materials than steel. However, steel is hard to come by and thus the prestressing braids are very strong. They have a breaking strength of 1860 MPa. To compare, Titanium has a breaking strength of 1100 MPa. Also, carbon fiber is thought to be in its own class of 1500 – 2500 MPa, but prestressed steel is in the same strength class. The nominal breaking strength of standard reinforcing steel is 550 MPa. Hence, the prestressing strand is more than three times stronger!
However, hollow core slabs are not always used as horizontal structures. They can also be installed vertically as outer walls, dividing walls and noise barriers. This is enabled by the long spans and durable structure. Hence, they are especially beneficial for industrial buildings, where a high unified space is needed. On the other hand, the slabs are highly resistant to changing weather conditions and have efficient noise reduction, which makes them ideal noise barriers.
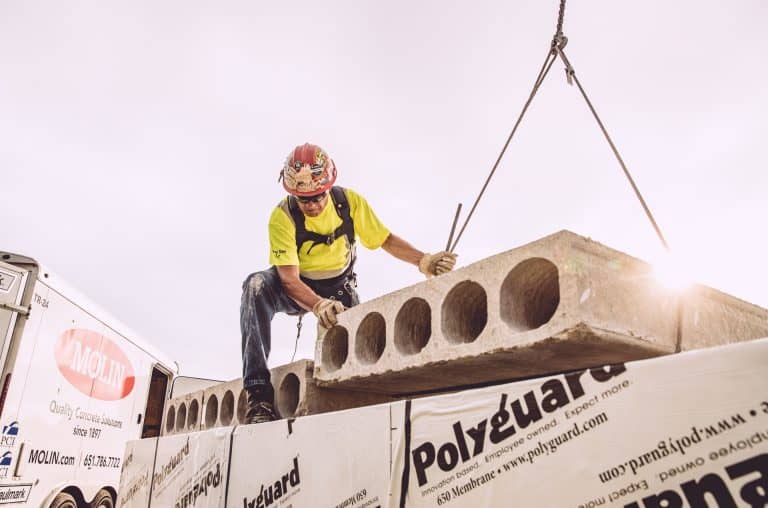
Efficient use of floor area
Not only do hollow core slabs enable construction of versatile buildings, they increase the usable floor area. How? The span of a hollow-core slab can be even up to 20 m without intermediate supports, which results in spacious rooms with less partition walls.
Think about it: if long-span hollow-core slabs are utilized for the floor of residential buildings, non-load-bearing partition walls can be placed inside of the flats. This gives freedom to the architects, because the floor layout can be easily modified. To enable this, the structure of the building should be designed so that the slabs are longer than the rooms or even apartments. Likewise, in commercial and public buildings, long-span hollow-core slabs enable less inner supporting structures, e.g. pillars, which can be rather annoying, for example, in parking halls. Thus, architects and structural designers have more freedom in designing well-functioning and visibly appealing spaces.
Moreover, the decreased need for load-bearing partition walls and columns results in lighter structures. Therefore, the weight of the whole building is reduced, which results in smaller and more affordable foundations. This is especially beneficial when designing and constructing buildings in seismic areas, because earthquake forces are proportional to the weight of the structure.
Increased sustainability
In general hollow core slabs are one of the most sustainable products in construction, because less material – less cement, less water and less steel – are needed for manufacturing them compared to cast-in-situ. Also, the voids of the slabs make the production more material-efficient. This result in lighter slabs, which decrease the transportation costs as more slabs can be delivered at once in comparison to, say, solid slabs.
The entire structures built with hollow core slabs also have a longer life span, because slabs won’t crack under service loads and all the reinforcements are protected from corrosion. So, if you think about it, the world is in demand for sustainable and durable construction due to population growth, extreme weather conditions and seismicity. Hence it only makes sense to design buildings that will last the test of time. After all, sustainable development is supported and even required by varied stakeholders; the governments, citizens and other companies in the construction industry.
To sum up, the question is not so much about why to use hollow core slabs, rather why not to use them? Hollow core slabs are very well tested – 1,000,000,000 m² = one billion square meters of hollow-core slabs have been estimated to be installed in Europe alone – secure and safe solution. I think that choosing precast benefits all the parties: the contractors, developers and people working and living in the buildings.
If you want to learn more about how hollow core slabs can be used, I and my colleagues at Elematic are happy to help.
Writer
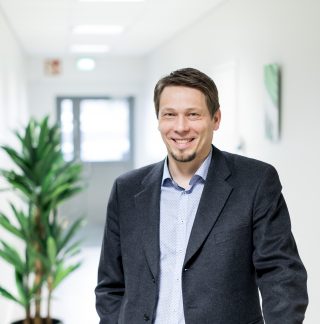
Jani Eilola,
Product Director, Floor Technologies
Elematic