How to save cement in hollow-core slab production?
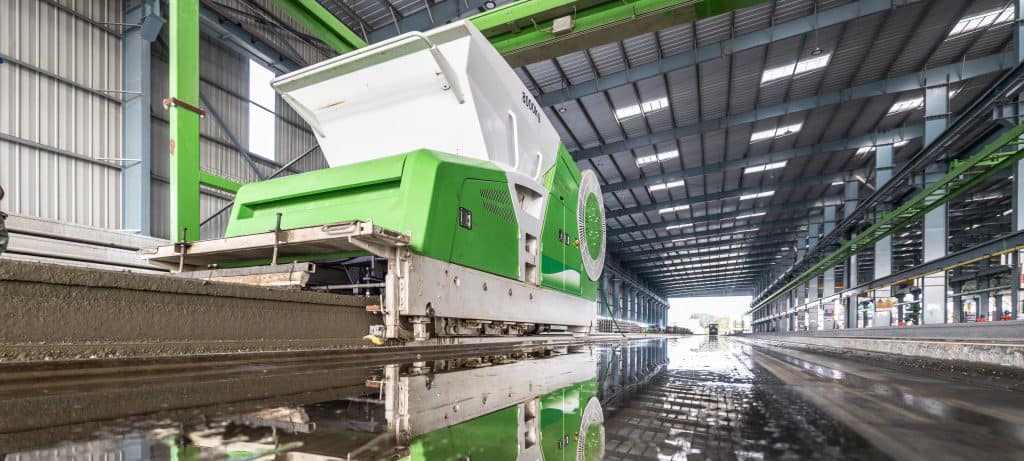
Have you pondered how to increase the productivity of your precast plant cost-efficiently? How to save cement and assure capacity of your hollow-core slab production? If yes, read how a modern shear compaction extruder was developed and how it nowadays positively impacts hollow-core production.
If the history of your plant dates back to the early 20th century, they may have started hollow-core slab production with slipformers or machines featuring the ‘’tube pull’’ method. They were the only options in the 1930s. About 30 years later, the first step towards more efficient production was taken with a vibrating extruder. In 1971 Elematic – Toijalan teräsvalmiste at the time – presented their first vibrating extruder.
But how do vibrating extruders work? They have an electric motor, which rotates the eccentric, resulting in a vibration frequency of 50 – 250 Hz. This method offers easy production with efficient compaction, but has several downsides. The quality is inconsistent, the noise levels are extremely high and the machines are prone to breakdowns. Even so much so that – in the worst case – your production slows down and you lose bidding competitions against your competitors.
Back in the 80s, we wanted to change the situation, so we came up with the first ever shear compaction extruder in 1985. Ever since, machine manufacturers have preferred the shear compaction method due to the many benefits it brings to the factory.
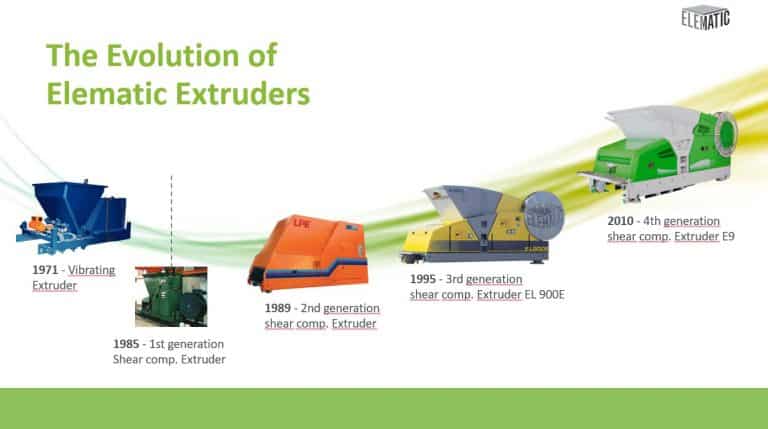
How does the shear compaction work?
How does a shear compaction extruder work? The concrete is compacted by the means of a controlled three-dimensional motion. The compaction frequency is approximately 10 Hz. It is considerably less compared to vibrating extruders. Efficient feeding screws also play as essential role. They push the Extruder forward on the casting bed while compacting concrete.
Over the years, the shear compaction technique has been greatly developed. Today it’s the ultimate choice for cost-efficient production of hollow-core slabs. If you are interested in setting up your first hollow-core factory or looking for more efficient production methods, your needs have been heard with Elematic Extruder P7. It uses shear compaction technology, and it moves along the bed, freshly cast slabs with exactly required dimensions and smooth surfaces are left behind.
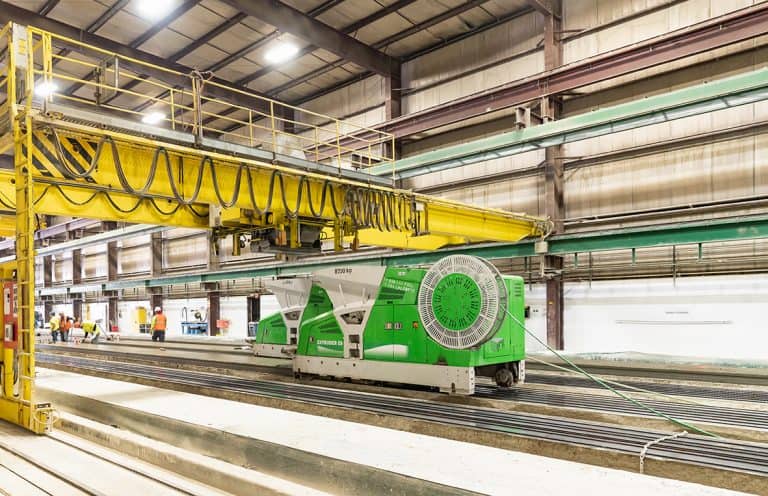
Consistent quality with automatic compaction
No matter how good your B & M plant is, it’s not possible to make 100 % similar concrete batches every time. There will be fluctuation from batch to batch, which affects the workability of concrete. This is where automatic compaction will help. Automatic compaction control senses the consistency of the concrete by measuring the resistance from the screws. Based on the information the casting parameters are adjusted: braking, “pulling”=assisting movement, shear compaction movement frequency and screw speeds. This ensures constant compaction and cohesive quality of the produced slabs.
What’s the biggest advantage of efficient compaction? You will considerably save cement as significantly less cement is needed to fill the spaces between the aggregates. For example, compared to a slipformer, you will need up to 30 % less concrete and save up to 150 kg / m³ of cement. Extruder E9 2010 has 10 – 15 % more efficient compaction and saves 15 – 50 kg / m³ of cement compared to the older Elematic Extruder EL 900.
NOTE! The density of concrete has an exponential effect on the strength. 5 % reduction in the compaction means over 30 % reduction in the strength!
Also, you may have spotted that problems sometimes arise because of a change in resistance due to friction from the strands, or a change in the concrete amount in the hopper. These problems can be avoided with automatic compaction. It resists or assists the extruding movement, whichever is needed at a given moment.
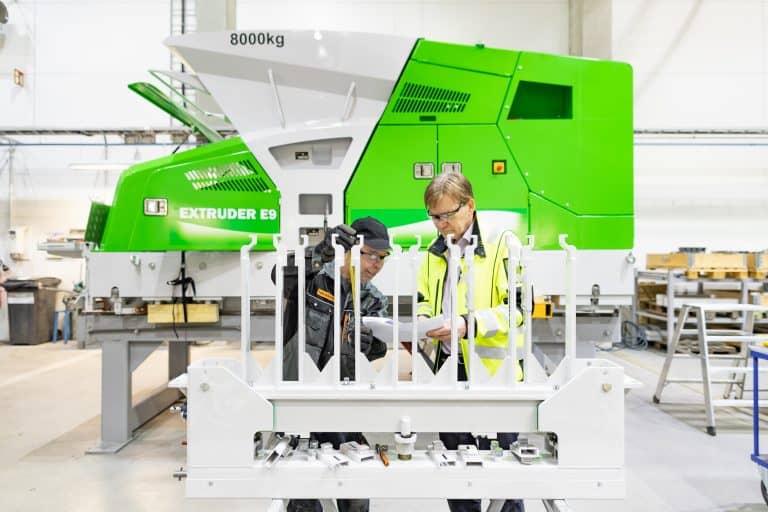
The machine design matters
Comparing to the old Elematic EL900, and other extruders on the market, the Extruder P7 has a more rigid frame. Thus the frame does not give in and the power goes to the concrete. The rigidity is achieved by using cast parts instead of parts made out of steel plate.
In addition, if you want to produce slabs with different cross sections, several nozzle units are available and we can advise you on the most suitable one. Also, if your customers need slabs of different heights, you can meet the need with P7. It is designed for casting slabs of up to 500 mm high.
Efficient compaction means less strand slippage and more geometrically perfect slabs. You will also significantly save cement and decrease the amount of production errors. Your customers will thank you for fast deliveries of high quality slabs and thus you will win more projects in the future.
Writer
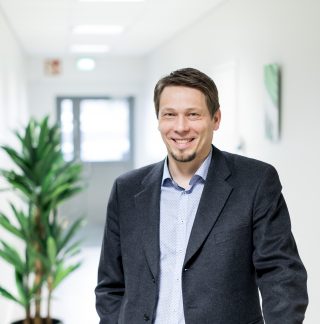
Jani Eilola
Product Director, Floor Technologies
Elematic