Why preventive maintenance pays off in precast concrete plants?
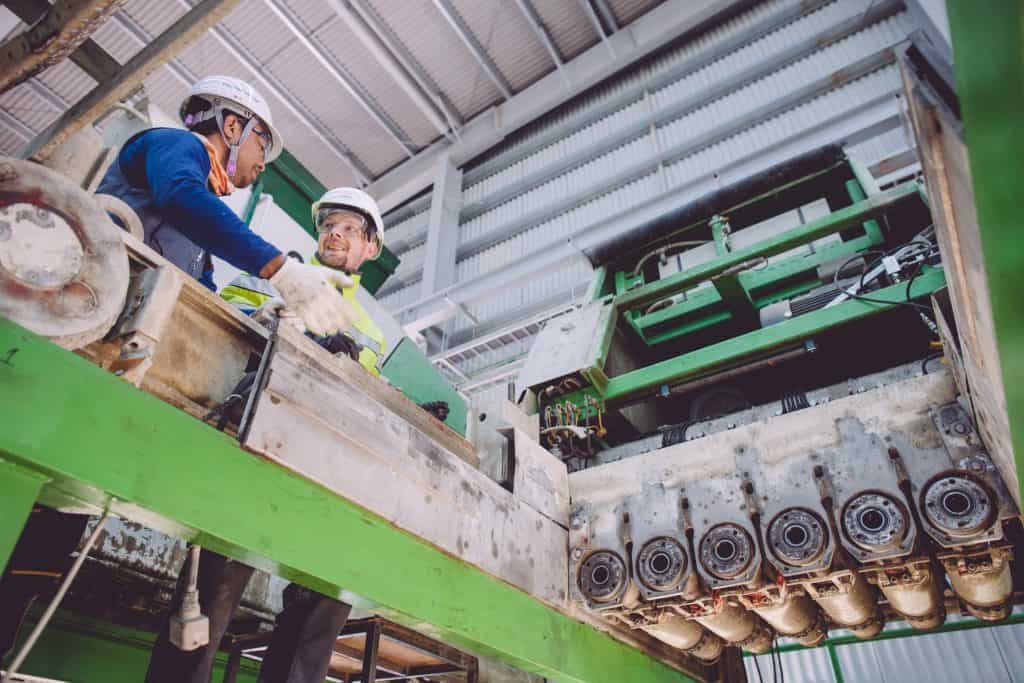
Do unforeseeable factory downtime and the costs of such surprises annoy you? Do such maintenance breaks negatively impact your production schedule and the satisfaction of your clients? Would you like to get rid of these problems? It’s possible with a preventive maintenance program that covers the whole precast plant. Let’s take a look at why such a program makes a big difference to your precast business.
First things first
Is your precast equipment cleaned daily? If not, this is the first habit that would benefit you in the long run. Why? When the machinery is washed at the end of each manufacturing day, there won’t be any dried up concrete stuck on the machine. This not only makes your life much easier but also keeps the machine in good condition much longer. While you are washing the machine, it’s also easy to conduct the daily check-ups at the same time. What’s more is that we humans tend to respect clean and maintained machines more compared to the ones we consider old or already broken.
Also, it’s important to have trained staff that knows how to use the machinery and knows when something is not working as it should be. For example, a well-trained employee knows when they hear an unusual sound. They understand that the casting should be stopped and the machine checked immediately. If production is continued without any check-ups, it is likely that you face a machine breakdown and a production stop, even if originally only some simple adjustments were needed. Prevention is always cheaper than repair; hence the machinery should be kept in a good condition.
But daily check-ups are not enough to avoid production downtime. A well-planned maintenance program is needed to keep the machinery up-to-date for years to come.
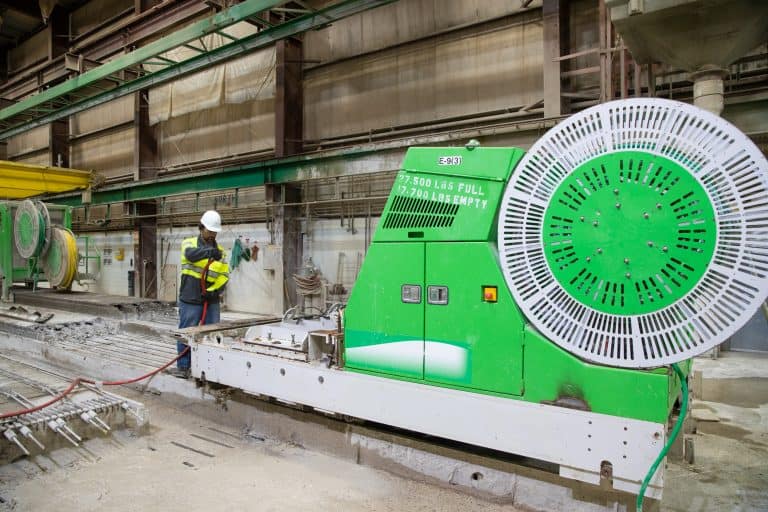
Maintenance program
Do you have a preventive maintenance program for your precast plant? During the 60 years in the precast business, we have learnt that having an efficient maintenance program is the key for cost-efficient production. Thus, if you don’t have it in place already, we recommend that you create one now. It’s not cheap if an extruder breaks down in the middle of a casting bed. You will be paying for your employees just to stand and wait for the machinery guys to finish their job. And when you can finally start casting, you need to prepare the beds again, which also adds to costs.
When you have an efficient preventive maintenance program in place, you will avoid such a situation. Instead, you can schedule a maintenance break for an extruder to a time when all necessary casting can be conducted with another machine. You can also ensure that a trained maintenance team and tools are available. During the maintenance, the machine can also be adjusted if needed, according to the casting requirements. We are happy to give you advice about how to go about it, or a ready-made program through our service agreements.
We have made some recommendations for maintenance in the Elematic equipment owner’s manuals. You have received them in print format, but they can also be accessed online through the spare parts web shop – E-shop. However, these recommendations are only general guidelines, because each factory is different and, for example, used stone materials affect the durability of the parts differently.
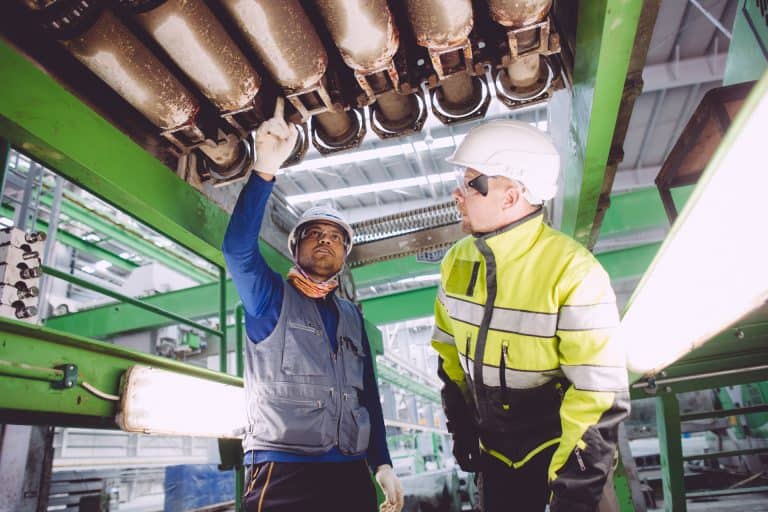
Stocked spare parts
We advise you to stock a selection of spare parts at your precast plant. Even though they can be quickly ordered from Elematic sales engineers or through E-shop, the delivery will always take some time. After you’ve used to a specific machine, you will notice how often certain spare parts need to be changed. Hence, you can have a few of them stocked to avoid factory downtime. It’s also good to be prepared for accidents. For example, every now and then we hear stories about someone accidentally mashing the touch screen of the machine. The screens are basically the hearts of electrical automation features; hence it’s advisable to have one screen in stock just in case.
In addition, it’s extremely important to change spare parts in time, because over-worn parts can decrease the quality of your slabs and damage the machine.
Preplanned maintenance breaks boost the efficiency of your factory and create a safer working environment for your employees! If you have any questions about preventive maintenance programs, spare parts or anything alike, I am happy to reply.
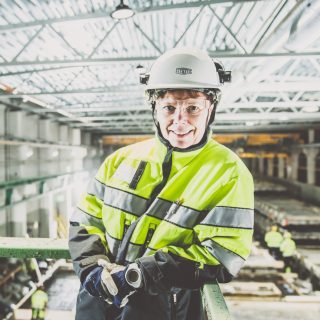
Eija Aimolahti
Customer Support Manager
Elematic