Install up to 90 sq. m of partition walls in 8 hours. Acotec technology comes with many benefits.
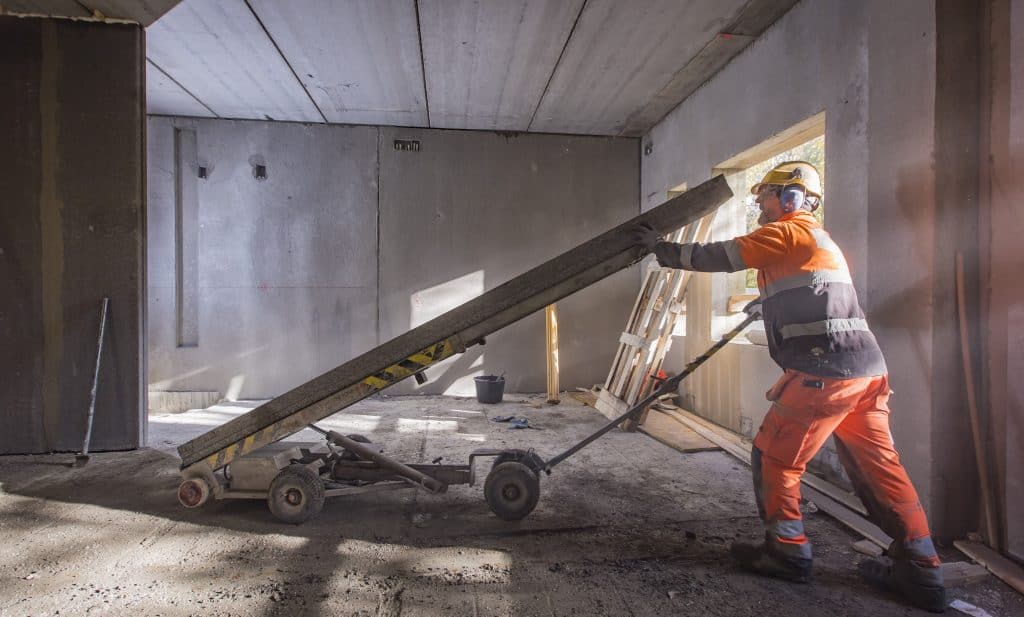
You may have stumbled across Acotec panels before – or it may be a new building technology for you – but if you are making partition walls out of tiles, bricks, gyproc or calcium silicate panels, this is for you!!
What is Acotec?
The word Acotec carries a double meaning. Firstly, Acotec refers to light, non-load bearing partition wall panels. Secondly, Acotec refers to the technology, or the production line, with which those panels are being manufactured. In this blog, I will describe a bit of both but let’s take a look at the panels and their characteristics and usage first.
Where to use Acotec panels?
You can use Acotec non-load-bearing precast partition walls in apartments, but they are also suitable for many other building types. The Acotec panels provide excellent sound insulation up to Rw 48 dB; hence the panels can be used in buildings with high sound insulation requirements. Fulfilling the set fire resistance requirement isn’t a problem either; the thickest panels can hold fire for up to 120 minutes (corresponding time for the thinnest panel is 30 minutes). You can also use the Acotec panels for wet rooms as they have top-rate moisture resistance.
What’s the size?
The size of the Acotec panels can vary; they can be 2.2 to 3.3 m long, 60 cm wide and 68 to 120 mm thick. Their weight depends on the thickness and the concrete mix used. When using Leca concrete, the thinnest panel weighs approximately 62 kg/m² and the thickest about 110 kg/m². If normal concrete is used, the corresponding weights are 80-95 kg/m² and 150-165 kg/m². The heaviest panel can weigh up to 220 kg/m.
How to install?
Installing the panels is cost-efficient and quick – you can install up to 90 m² per 8 hours due to the standardized shape and light structure. The installation begins by lifting the panel to an upright position to its addressed place. Next the panel is cemented to the floor and to the ceiling. Sealing the ceiling joints happens with urethane and the gap between the panel and the floor is filled with mortar or concrete. When you want to connect an Acotec panel to the exterior wall, the gap is sealed with an elastic putty or acrylic paste. Lastly, you will do skim coating before the surface is finalized. In sanitary facilities, the skim coating must be water-sealed. Moreover, when using Acotec panels you can install electrical wires and water pipes to the existing cavities, which work as a practical duct.
How to move?
Now you may be wondering how the panels can be moved around while the construction work is ongoing. Let me tell you that the simplest method is to lift the panels close to the installation place before the next floor is built up or alternatively lift the panels in through openings, such as windows and doors. You can lift the panel stacks from under the wooden pallet with a lifting fork or belt.
If you have already built the next floor, the panels can’t be directly lifted to their optimal places. In this case the Acotec Installation Wagon may be of your interest, because it is ideal for moving the panels around in the floors and lifting them to an upright position. Other alternatives include using some kind of a trolley or carrying the panels by hand.
Note! The panels must be stored on their sides at all times and I suggest you to store them in their packaging plastic until installation. However, keep in mind that the plastic film has to be removed 1-2 days before installation to allow the panels to dry.
Now let’s take a look at the production side of the Acotec panels. What is it that you should be aware of if you are pondering whether to start producing Acotec panels?
What is needed for setting up Acotec panel production?
The Acotec production lines do not require much land area, so finding a suitable location for the factory is relatively easy – and also affordable. The production hall for the line should be 1,000 m² and have a free height of 5.5 m. You will also need to have 2,000 – 4,000 m² reserved for the concrete mixing plant, storage and office. Of course, you will need electricity and water: The switching power without the concrete mixing plant should be 50 – 60 KVA and the water consumption will be around 1.5 m³ per an hour for producing 4 – 8 m³ of concrete in the same time frame.
How’s Acotec businesswise?
With Acotec, you will be changing low-cost or bulk -materials into high-processed products of high added-value. If comparing with calcium silicate solution, for example, you can notice a clear difference in the materials used. In the calcium silicate solution, you will need to purchase materials which have already been processed, but with Acotec, you are doing the processing and thus adding the value yourself. For Acotec wall production you will only need simple basic materials – aggregates, cement, sand and water – which are easy to get and affordable. No admixtures are needed. Even the water doesn’t need to be drinkable as long as it is clean enough. This leads into good profitability as purchasing unprocessed materials tends to be less expensive compared to the alternative.
Another aspect covers the production capacity and investment size. You can start producing Acotec partition walls with a relatively small budget and expand the production if the need on the market exceeds the production capacity. This is a clear advantage, as setting up a gyproc wall production line, for example, requires a larger initial investment and land area; hence the associated risks are higher as well.
Where to get the technology?
You can get the production technology from Elematic. Our SEMI, PRO and EDGE lines offer different options in production capacity, automation level and number of personnel needed to run the line. The production process is always the same, only the level of automation varies so the decision depends solely on your requirements. . If you decide to go for the EDGE line, the employee requirement is 1 – 2 people. However, with the SEMI line, you need to hire seven people.
What’s the production process?
The Acotec line covers the entire production process from concrete batching all the way to storage yard management and beyond. The panels are formed in a continuously operating extruder that compacts the concrete with extrusion screws against the packing bar and sidewalls. The top surface of the product is vibrated by a vibrating plate. This method allows you to adjust the optimal compaction level, so that the panels will be of high strength and can be cut immediately but still remain light-weight.
Overall, you can reach multiple benefits by making a decision to produce Acotec wall panels. The lines can be modified to meet needs in your market area and are easy to set up. The production itself is straightforward and great profits can be reached by changing bulk materials into products of high added value. After the fast and easy installation of the panels that makes the builders happy, the end-user of the building will also be pleased of the noise, moisture and thermal resistance of the Acotec panels.
Concentrating on the actual business is easy with Acotec from Elematic.
Writer
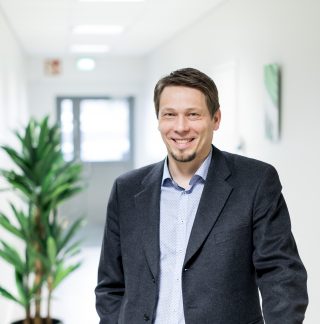
Jani Eilola
Product Director, Acotec and Floor Technologies
Elematic