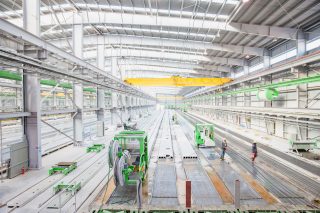
Precast concrete plants: 5 tips for an efficient project
Are you planning to establish a precast concrete plant? But are you perhaps still a bit unsure how to proceed, what…
Often questions arise about the construction of a certain number of villas in a specific time frame or the construction of affordable residential houses of specific size per one or five years. In this blog, I will go through the key issues relevant to building villas using precast concrete technology and how we can help you in reaching your goals and overcoming any potential problems along the way.
This blog discusses precast concrete technology from the point of view of constructing 1,000 villas in one year. For such a project, in addition to cost savings, speed, quality, safety and sustainability are the benefits reached with precast in comparison to cast-in-situ.
The pictures on the right are a great example of the effectiveness of precast concrete technology, because they illustrate the difference of constructing a villa with the same design using the cast-in-situ method versus precast concrete technology. The differences can be discussed through four main perspectives:
1. Speed. Precast construction enables you to build more villas in the same time frame compared to using cast-in-situ, bricks and blocks; precast concrete is an industrialized way to build. Because precast components are manufactured at factories, the need for manpower decreases at the construction site. Approximately 50% less manpower is needed while precast panels are assembled two to three times faster.
2. Quality. Producing precast panels at a factory results in consistent quality, not to forget about precast’s sound insulation and fire resistance capabilities. Global, regional, and national design principles and standards also help maintain and further develop the quality.
3. Safety. Factories are controlled environments, where the machine and employee safety have been thoroughly considered. In addition, fewer people at the construction site equals to lesser chance for accidents to occur.
4. Sustainability. The main benefits come from the saved materials; roughly 20-30% of steel and cement can be saved by opting for precast instead of cast-in-situ, and energy efficiency which is better throughout the villa’s lifetime. Note-worthily, cooling down a building is two and a half times more expensive than heating up a building, and thus, it is very important also for warm countries to have proper insulation.
The above mentioned are the basic benefits that we have recognized and calculated all over the world – benefits that also construction companies and developers have acknowledged when changing to the precast technology. The benefits also come with a decrease in costs: time saving, optimal use of raw materials, manpower needs, energy-efficiency of precast buildings and durable construction.
I will introduce a cost analysis of 1,000 one-story villas made for a real project that gives you a better idea of the precast building components needed and their costs.
For the built-up area of 169,000.00 m2, 180mm thick load-bearing insulated wall panels with a grey concrete mold/trowel finish, 150mm thick solid wall panels with the same finishes, 120mm thick solid wall panels with the same finishes, 150mm thick hollow-core slabs and 200mm thick hollow core slabs are needed. For these, the approximate price is 167.23 dollars per m2 including factory, delivery, erection, and crane costs. For the foundations and grade slab 250mm thick precast concrete footing with a grey concrete mold /trowel finish, concrete grade beams with the same finishes, and 150mm thick hollow core slabs are needed, costing approximately 137.99 dollars per m2. All the finishing works et cetera are excluded from the prices – the prices cover the frames and the foundations for 1,000 villas.
Ismo Kallio, Vice President Sales
Elematic
Let others enjoy this blog too:
To manage the precast construction of 1,000 villas in one year, we suggest a precast plant with a production capacity of 1,126 m2/day of hollow core slabs, 585/205 m2/day of load-bearing insulated/solid walls, 230 m2/day of non-load bearing walls and 360 m2/day of foundation parts. This production capacity easily allows producing 1,000 villas in a year. Setting up such a precast plant takes approximately six to ten months from signing the contract, including the design, manufacturing of factory equipment, transportation, and production start-up. In other words, you can produce the first panel in less than a year.
Regarding the manpower need, roughly five to seven people are needed for the hollow core plant and 30 +/- people on the wall side when counting reinforcements, depending on the complexity and type of the product you are producing.
Before setting up a precast plant and starting a precast construction project there are several key factors that are beneficial for you to know and plan. It is worth remembering that the key factors should support one another. For example, when designing and manufacturing precast components, the lifting capacity and condition of the roads should always be considered. In other words, it is important to plan efficiently and in a detailed manner to have a smooth process from the planning to the assembly. I and my colleagues at Elematic are happy to help you in reaching all the following key success factors, with our over 60 years of experience in the precast business, from your initial interest in precast to the lifetime of your precast plant.
– Feasibility study of the project
– Architectural design
– Selection of building system
– Conceptual design
– Detailed precast panel design
– Project planning
– Production planning
– Production in the factory
– Transportation to the site
– Assembly and other site work
– Teamwork and cooperation (I consider this as one of the most important lessons-learned for a successful project)
Building Information Modelling (BIM) is one of the key issues, because it enables efficient management of all the design phases from the overall design to smaller details. In addition, BIM provides efficient information sharing between design, production and construction, thus enhancing collaboration.
If constructing precast villas or precast technology in general intrigues you, read more about how to adopt precast concrete as your building technology here or send us your questions with the contact form below.
My colleague, Curt Lindroth, also recently introduced precast construction of luxury apartments, Grand Views in Dubai, which might be of your interested: Luxury apartments built with precast concrete in Dubai
Are you planning to establish a precast concrete plant? But are you perhaps still a bit unsure how to proceed, what…
Would you like to set up a precast plant, but aren’t quite sure of the schedule? Are you uncertain of which…