3 tips for easy automation for hollow core factories
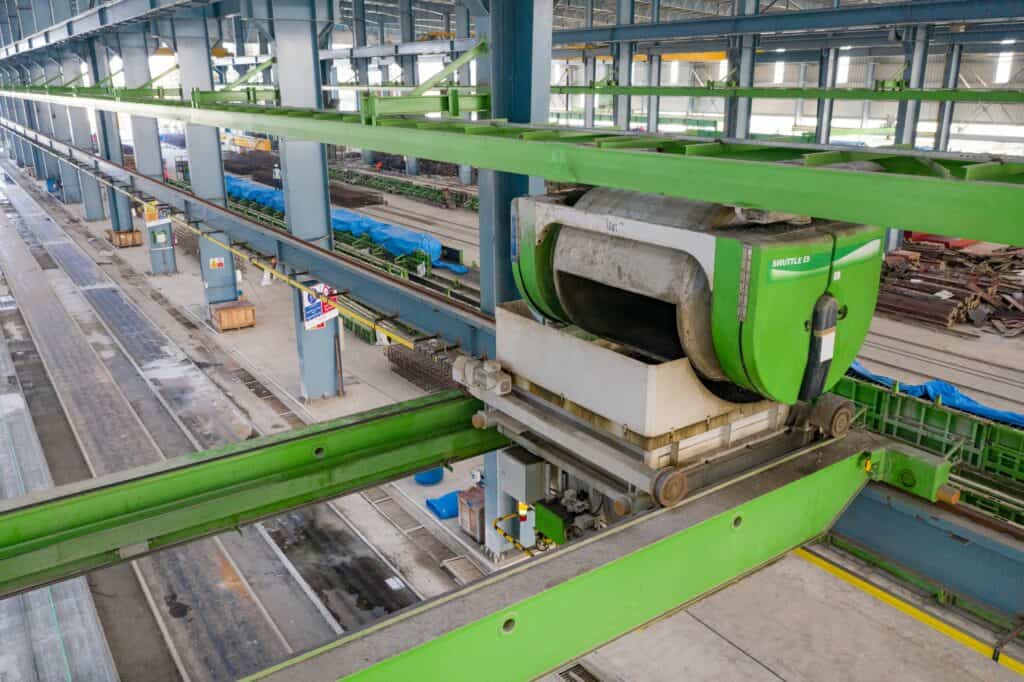
Automating your precast factory operations does not necessarily require a lot of digitalization. Some steps of the precast production can be easily automated and implemented, as long as you have electricity.
Despite your hollow core factory’s current automation status, you might have considered automating some production process steps. Automation at its best increases safety, decreases human errors, and saves time. Also, automation can be easy. All you need is electricity.
Let’s look at how to speed up precast production with simple automation.
Fast and reliable concrete transportation
Distributing concrete from batching & mixing plant to an intermediate silo or directly to casting spots can be done in a fast and reliable way with automatic transportation system with tracks, conveyor and shuttle. In many precast factories, concrete is transported with forklifts and concrete buckets to casting spots, lifted with a crane, and poured on the extruder. These work phases are heavy, take time and require manual labor. Automatic concrete transportation system can be adapted to existing B&M plants. The digital bed plans are not needed and yet there’s a big step forward in automating the production process.
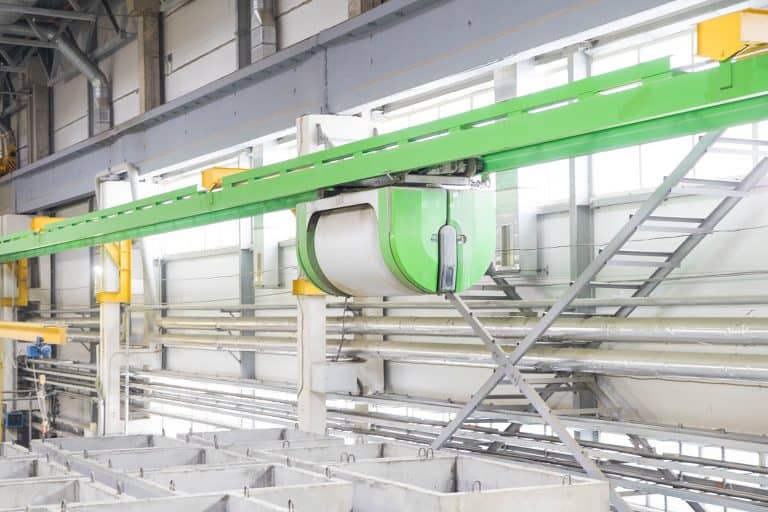
Ensure concrete quality and consistence
Each concrete batch can differ slightly from each other. For example, the aggregates cannot be weighed 100% accurate, and water dosing can also deviate a little and affect the quality of the slab. By investing in casting machine that can automatically recognize the variations in concrete quality, the slab quality increases. For this specific need we have developed the Extruder E9. It is equipped with that sensors recognize when there are changes in concrete quality and automatically adjust the concrete feed parameters accordingly.
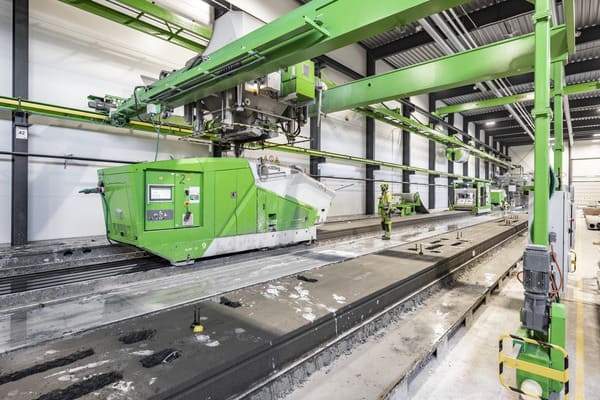
READ MORE ABOUT THE EFFECTS OF CONCRETE TO SLAB QUALITY
Fluent slab transportation
Sometimes there can be peaks in slab loading at the storage area, which can delay moving the slabs from production to the storage area. Production might be delayed, even stopped, because the beds can’t be emptied fast enough. Solution to these bottlenecks can be trying to optimize the slab pick-up times from the storage, have more efficient hollow core slab transportation from beds to the storage area, or investing in an additional crane.
The automated E9 wagon helps to move the slabs quickly from production to the storage area: you can empty the bed on the wagon and move the slabs automatically to the storage. The transportation system consists of active and passive wagon with combined 30 t capacity. Factories who are producing shorter and relatively light slabs can add more than one passive wagons in the system. Compared to our previous wagon model, automated and battery-driven E9 wagon helps to get rid of the cable and it can use the same tracks. The wagon has sensors that guarantee safe movement, and it is an exhaust-free option for slab transportation
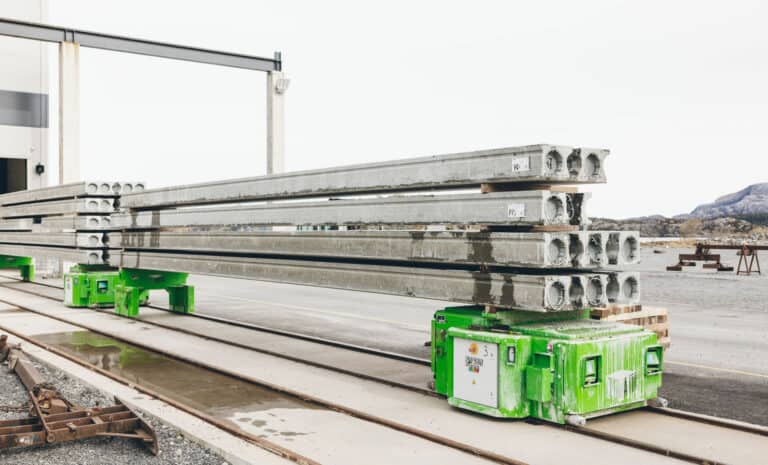
Before investing in any automation, the production bottlenecks should be identified. What is the best solution for your operations?
Writer
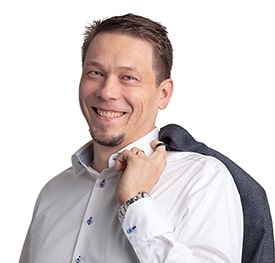
Jani Eilola
Product Director Floor Technologies
Let others enjoy this blog too