Wastewater device is ready for the market
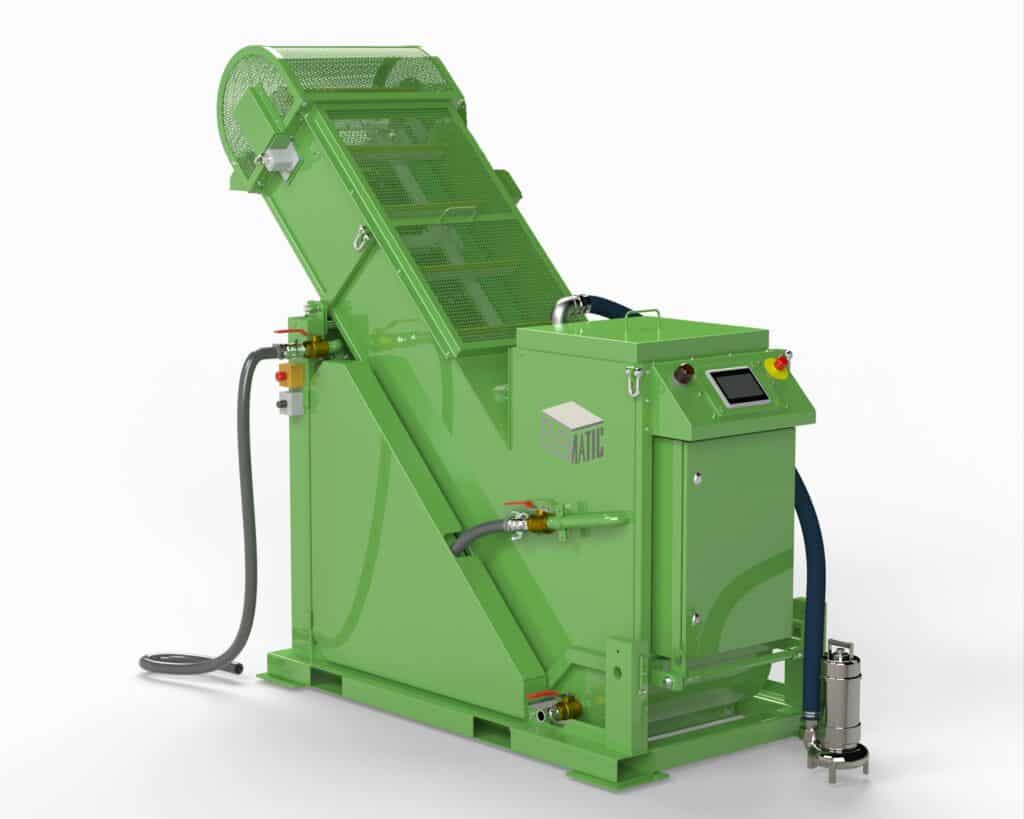
After thorough testing at Lujabetoni’s plant, Elematic is ready to ship automatic wastewater recycling devices to precasters around the world. The two inventors are proud, excited – and a little anxious.
A new Finnish invention, a small-sized, fully automatic wastewater recycling device for precast plants, has for almost two years been tested at Lujabetaoni’s precast and ready-mix factory Hämeenlinna, Finland.
Elematic has included the innovation in its offering, and is now, after the successful testing period, ready to deliver the device.
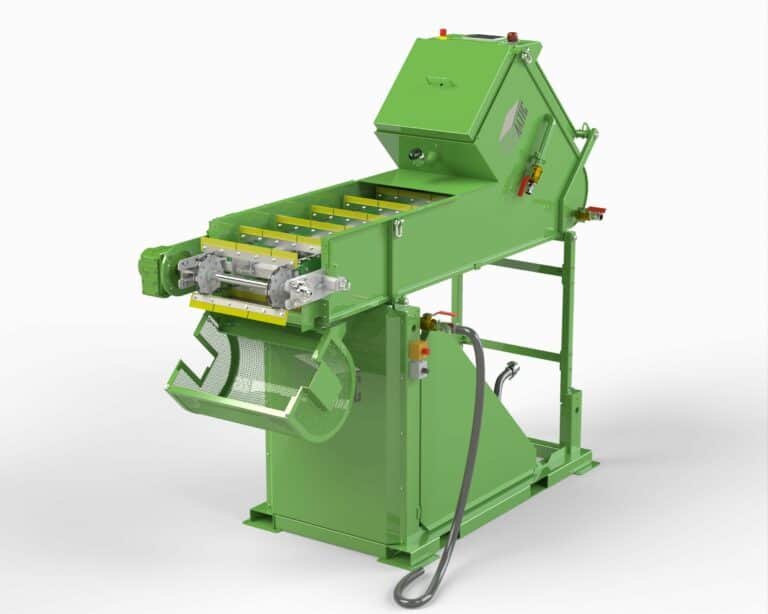
Precasters by day, inventors by night
More than seven years ago, Jussi Alatalo and Teppo Kasanko set out to solve the problems they experienced with excess or poorly filtered wastewater at precast concrete factories.
They would meet after normal work hours to develop the innovation. “And then we’d both get caught up by an eager enthusiasm and suddenly it would be three o’clock, and we’d have three hours of sleep left before the next workday began,” Kasanko remembers.
The fruit of their side hustle was a compact, automatic wastewater recycling device with a very fine filter that separates solids and water for recycling.
When they started innovating, they were both working at Lujabetoni. Shortly after, Alatalo started his own firm, Tekivai.
“The idea was that we got to test our prototype at the plant for a while to see if the process worked as we hoped it would, but plans changed underway, as Lujabetoni wanted to keep the device,” Kasanko says.
He and Alatalo took care of the machine for the first year, until Elematic took over. Today, Kasanko is a project manager at Lujabetoni, while Alatalo runs his precast production equipment maintenance firm, Tekivai, and they function as consultants whenever needed.
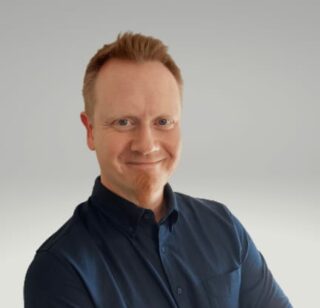
Teppo Kasanko
Cleaner water and less work
Lujabetoni’s factory in Hämeenlinna consists of three ready-mix batching plants and three production lines for precast frame elements and ducts. It produces 50-60,000 m3 of concrete a year and all wastewater runs through a large precipitation system.
Placing the compact wastewater recycling device before the last water basin has resulted in trouble-free wastewater recycling and freed up a big amount of man hours and thus costs. No more clogged water lines and excessive man-hours spent on digging solids out with an excavator.
Lujabetoni’s Production Manager Joonas Salmela and Service Manager Jouni Heikkurinen have followed how the wastewater device has worked in practice for nearly two years.
“Thanks to the device, we are sure to avoid clogs. We know that the process water that comes out of it is even cleaner than before,” Salmela says.
With a width of only 600mm and about two meters in height and length, the device is very compact. This makes it easy to integrate into an existing factory.
“We just had to install the electricity. After that it was basically plug-and-play,” says Heikkurinen.
Well-functioning prototype
The testing phase has gone well without any major problems, report Salmela and Heikkurinen, who have been happy with the close cooperation with Elematic.
The goal has been to improve the operational reliability of the final product, so the testing process has mainly been about observing how well different parts of the device worked. It turned out, for example, that stronger pumps were needed, and the filter types were also changed to optimize the process. This way, Elematic could be sure to choose the right components for the product before it hit the market.
“Some components have been changed, but we haven’t observed any fundamental problems with the technology. It works well,” says Salmela.
Heikkurinen adds that the maintenance requirements of the device have also been scrutinized. He praises it for being robust and simple to service.
“We’ve concluded that changing the filter and checking on the device once a week is sufficient. The rest of the time it takes care of its task reliably and automatically.”
After nearly two years of testing, the people at Lujabetoni would recommend the device to precast and ready-mix producers and any type of factory, where water is used for washing or cleaning, for example.
“Especially if you don’t have a lot of space, this system is perfect,” Salmela says. “This type of innovation is really needed as environmental requirements get stricter. As the water is cleaned better, water recycling is easier.”
Proud and anxious inventors
The inventors have happily followed the testing process too.
“The biggest surprise for us has been how well a prototype, only intended for short-time testing, has worked in real operations at a plant for nearly two years now,” Alatalo notes.
More than seven years after the first idea was born, the inventors are proud and excited about the idea that their “baby” is finally ready to go out into the world and make life easier at plants around the world.
“I’ve proudly shown Elematic’s product images to my family and friends,” says Kasanko. Alatalo adds that he is excited – and a little bit anxious – about how the market will welcome the device. They both agree that Elematic has done an excellent product development job.
“Seven years ago, we didn’t imagine anything like this. We only focused on solving one problem after the other. We didn’t really look at the big picture,” says Kasanko.
”It has been fantastic to realize that the machine that we designed and built works exactly as we intended it to.”
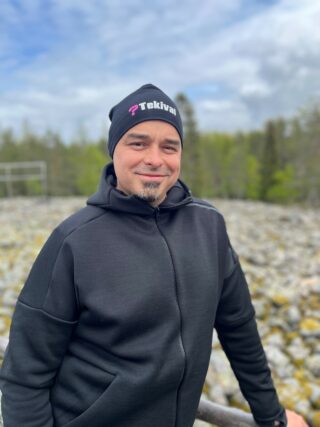
Jussi Alatalo
New wastewater recycling device
- Compact: 600mm wide and about two meters in height and length.
- Can purify 24 m3 of water per day depending on how dirty it is.
- Very fine filter – down to less than 10 ppm solid content, also fibers and EPS.
- The filter is automatically cleaned and can operate for about a week before it needs to be changed.
- The water is pumped into the machine where solids and water are separated before a scraper conveyer removes the solids settled at the bottom. The result is purified water and relatively dry sludge that can be transported for recycling with a regular truck.
Do you want to know more? Please, contact us!
or