How FaMe magnet shuttering system improves your precast wall production?
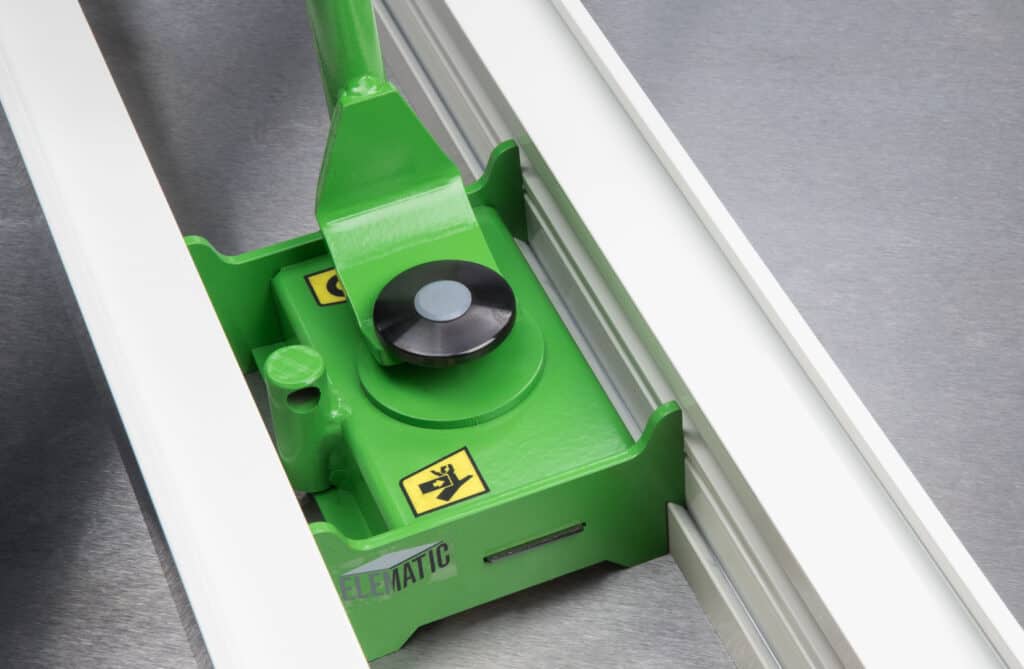
Would you like to make your wall production cost-efficient and safe? Elematic’s FaMe magnet shuttering system with push-button magnets and aluminum side forms suits table molds, battery molds, and column as well as pillar production.
If your goal is to produce straight-edged wall panels with low production costs, FaMe magnet shuttering provides the means. It is easy to attach and to remove from table surfaces. There is no need for welding, bolting or grinding, so your table surfaces will remain in good condition. And with the same frame system you can handle most wall thicknesses, from 70 – 500 mm, with accessories even up to 800 mm.
Steel and wood are commonly used as side forms in wall panel production – both of which have some downsides: steel is heavy and wood is thrown away after usage. With aluminum side profiles, you can save by decreasing the amount of waste wood. Aluminum is a recyclable material and you can cast directly on it.
If you cast with wooden profiles, it’s likely that the panels don’t come out as straight as they could because of the challenges with wood and water. It is hard to adjust wet wood side forms straight and in 90˚ corner. If you try to adjust them by hammering the magnet, it’s a health risk for both, the employee and the magnet.
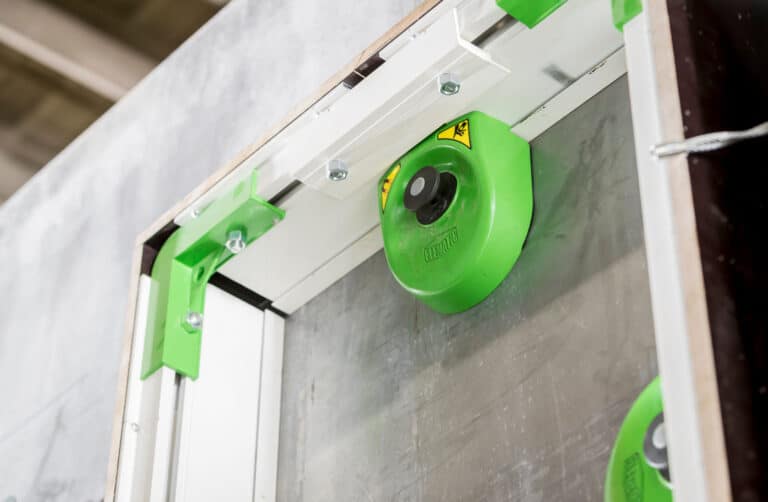
Safe and light system with free placement
The magnets and side forms are extremely easy and safe to use compared to other shuttering systems. The push-button and the housing of the magnet have been designed to give cover against any injuries when following the user instructions. The magnets’ green color works as an attention color at the factory hall. The aluminum side forms can be lifted without cranes; they are safe and light to lift with manpower. That helps to avoid bottlenecks in production.
The FaMe magnet shuttering system makes it easy to prepare the edges and window or door openings on tables or battery molds. You just put the side forms to the desired places and attach them to the mold with push-button magnets. The magnets can be moved easily by sliding them on the surface before pushing the button for attachment. The magnets can be placed wherever you want, because of the patented and compatible jaw groove of the side forms and the magnets.
To remove the magnets, there’s a releasing tool that you just attach to the magnet, then push the handle and remove the magnet from the mold. If you are new to using magnets and side forms in your wall production, we will guide you on the best working methods.
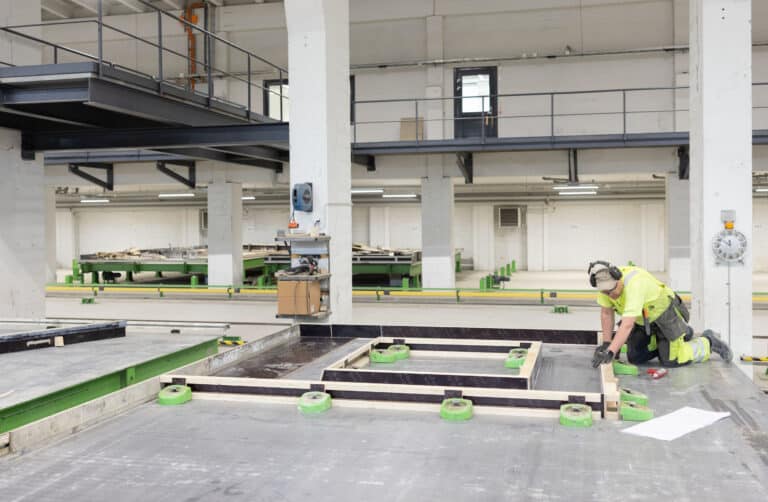
Regular maintenance guarantees long-lasting system
The magnets and side forms need maintenance just like any other machine. When kept in good shape and used as advised, the magnets will last for over a decade. What you should do is to always clean them after usage. Also, while oiling the molds, reserve some for the magnets as well for easier cleaning. The magnets can also be repaired if needed, spare parts are always in stock and ready for quick deliveries.
With FaMe magnet shuttering, you will have consistent quality of wall panels, safer working methods, and you will need to use less wood. You will save in production costs, your factory personnel will have safer equipment to use and you’ll have satisfied customers who appreciate the straight wall panels!
Share this article
RELATED PRODUCTS
ORDER OUR NEWSLETTER OR CONTACT US
or