5 key points of material technology in precast production
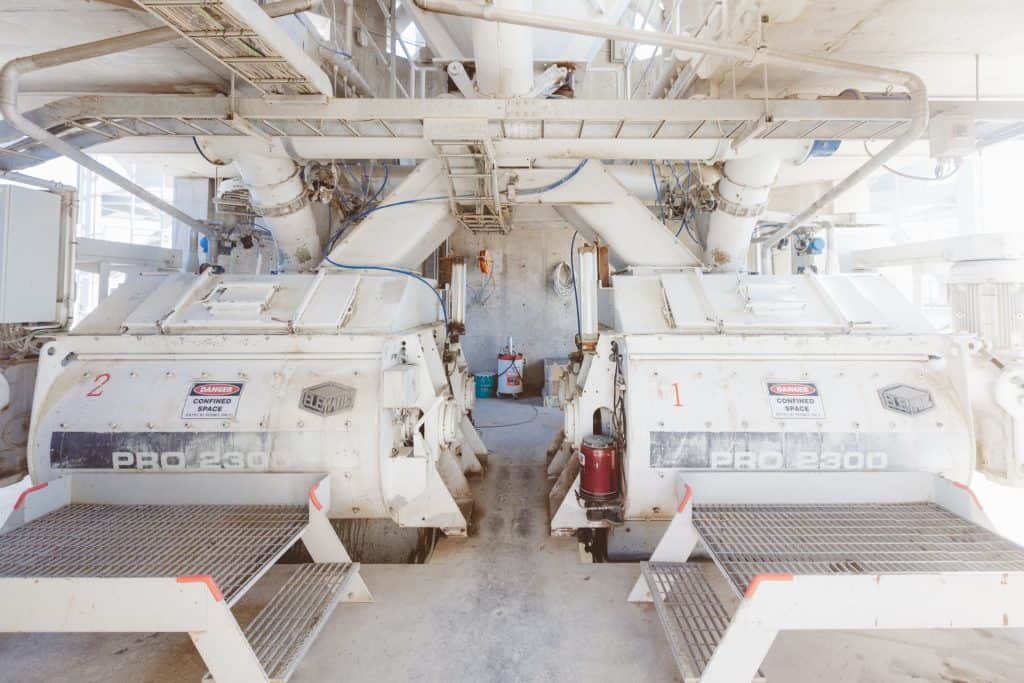
A good understanding and management of concrete technology are key activities in a successful precast production operation. As the primary raw material, concrete has a direct impact on the quality, production effectiveness and costs of precast products and structures. For every structure, concrete components must be adapted to the performance requirements of both, fresh and hardened concrete.
The following are the key points in the good understanding of concrete material technology.
1. Concrete is the key component in precast production
The visual (surface) quality of a precast product comes primarily from the concrete mix being used. Structural (load bearing capacity) quality also depends on the concrete mix. Furthermore, concrete is the main cost factor in most precast products. Even this is not all but the concrete mix and the related curing process define the achieved production cycle. Environmental matters are also of utmost importance and therefore concrete as a building material must be used as effectively as possible.
The main requirements and properties for concrete in precast are:
– Cost effective mix design
– Strength according to the design and other demands
– Fast and controlled hardening, importance of early strength
– Proper workability according to the casting method
– Good durability according to the design requirements
– Environmental aspects
2. Control the quality of raw materials
The composition of concrete can be described with the following picture where the material components are in volume %.
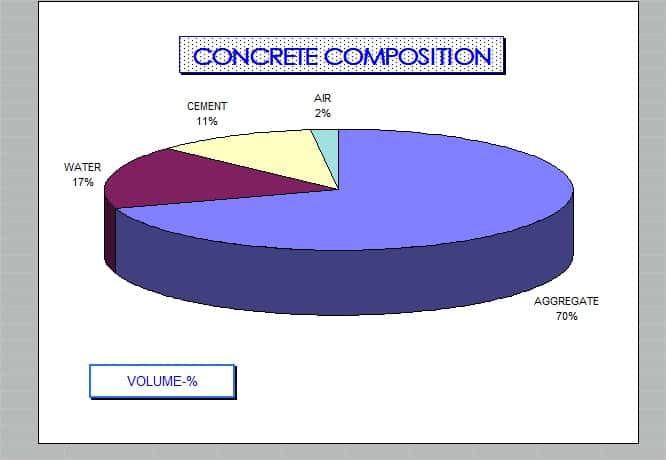
It is easy to notice the dominant share of aggregates. Aggregates are the strongest and most stable component and provide “the frame” for the concrete. Cement, in turn, can be considered as the glue between the aggregate particles.
In a concrete mix, we should maximize the volume of aggregates and minimize the volumes of both cement and water. However, aggregate is a natural material and the variation in quality and properties is therefore larger than with cement and its other components. This is why the emphasis in quality control in a factory lab should be on aggregates.
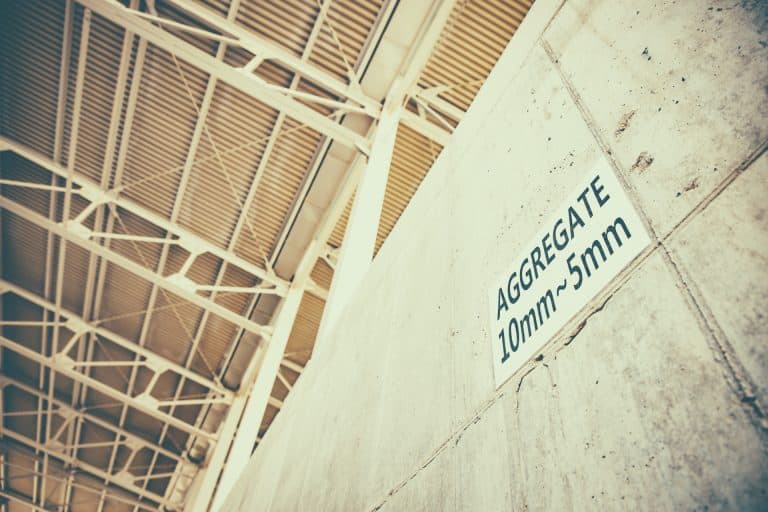
3. Cement is the key component
Cement is mostly the main cost in a concrete mix. The cement properties depend on the type of the cement, and it has a direct impact on the concrete properties. Cement factories typically give the main quality information on the cement being used. The use of different binder combinations can reduce costs and improve quality and can reduce the environmental burden of concrete. In the precast industry, early strength of the concrete is often the main requirement. The curing process is an essential part of the precast process.
4. Admixtures and additives are an important part of modern concrete technology
Admixtures are liquids or powders that are added to the concrete in small quantities during mixing. Their dosage is usually defined based on the cement content. Concrete admixtures can act chemically and/or physically, and they have a significant impact on the fresh and/or hardened concrete properties. Many admixtures can have several impacts on the concrete quality and these combined effects must be carefully checked.
Different (super) plasticizers are the most common admixtures in precast factories. They are used either to increase the compressive strength or to produce a more flowing concrete without any changes to the amount of water used. Other typical admixtures are air-entraining agents, hardening accelerators and retarders
Additives can be inactive or active. Typical inactive additives are lime fillers, rock flours (quartz dust, powdered limestone) and color pigments.
Mixes, where the amount of fines is low, can be improved by adding rock flours. These inert materials are used to improve the grading curve. The water requirement is higher, particularly with powdered limestone. Typically these materials are used in self compacting concrete.
Active pozzolanic or latent hydraulic materials, such as fly ash and condensed silica fume, as well as ground granulated blast furnace slag, are widely used in order to improve certain concrete properties or reduce the mix costs.
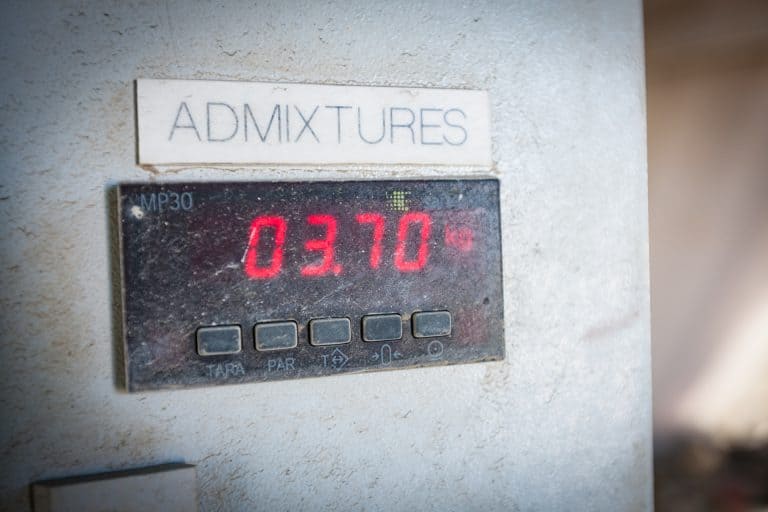
5. Curing process and maturity control are important phases of the production
In concrete, strength gain is the result of cement reactions with water, i.e. cement hydration. The hydration reaction generates heat, which further accelerates the reaction. The reaction can also be accelerated through the use of external heating. The hardening process can be measured as maturity. This, in turn, is related to the strength gain in concrete as a function of time and temperature.
By using heat curing, the early strength development in concrete can be controlled. The recommended maximum temperature of concrete is 60 C° (this value depends on the product and its use) with a 25°C/hour increase of temperature. A temperature difference greater than 20°C between the surface and the interior of the product increases the risk of cracking.
To achieve constant and consistent concrete quality, appropriate and correct curing is essential. The following curing measures contribute to this:
– Generally protect from adverse climatic influences (direct sun, wind, rain, frost, etc.)
– Prevent vibration (after finishing)
– Use a curing agent
– Cover with sheets or frost blankets
– Keep damp/mist or spray if necessary
– Maintain the curing time relevant to the temperature
There are several commercial methods for the overall curing process and related maturity control. The main target of these methods is to control and predict the hardening process. The other principal need is to have even distribution of heat/moisture during the curing process.
You might also be interested to learn more about how to save cement in hollow-core slab production.
Writer
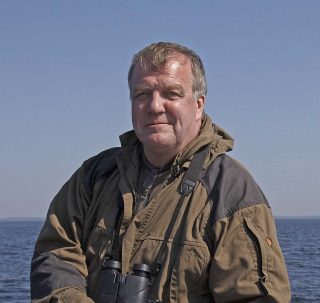
Olli Korander
Senior Advisor
Download full book “Basic concrete technology for the precast industry”
This book goes through all basics of concrete technology that a precast producer needs to know: raw materials, principles of mix design, concrete production, properties of hardened concrete, requirements for different concrete types as well as special aspects in concrete production and products.
Download your free copy now!
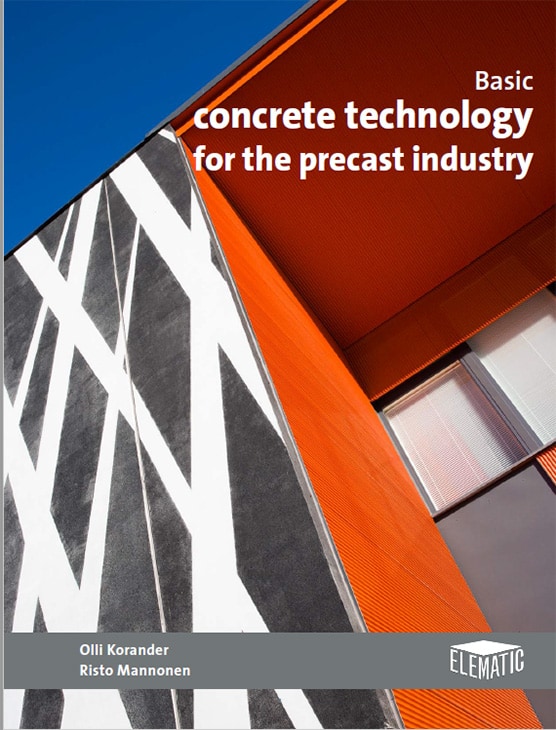