The potential value of digital situation picture in construction – What does it mean for a precast producer?
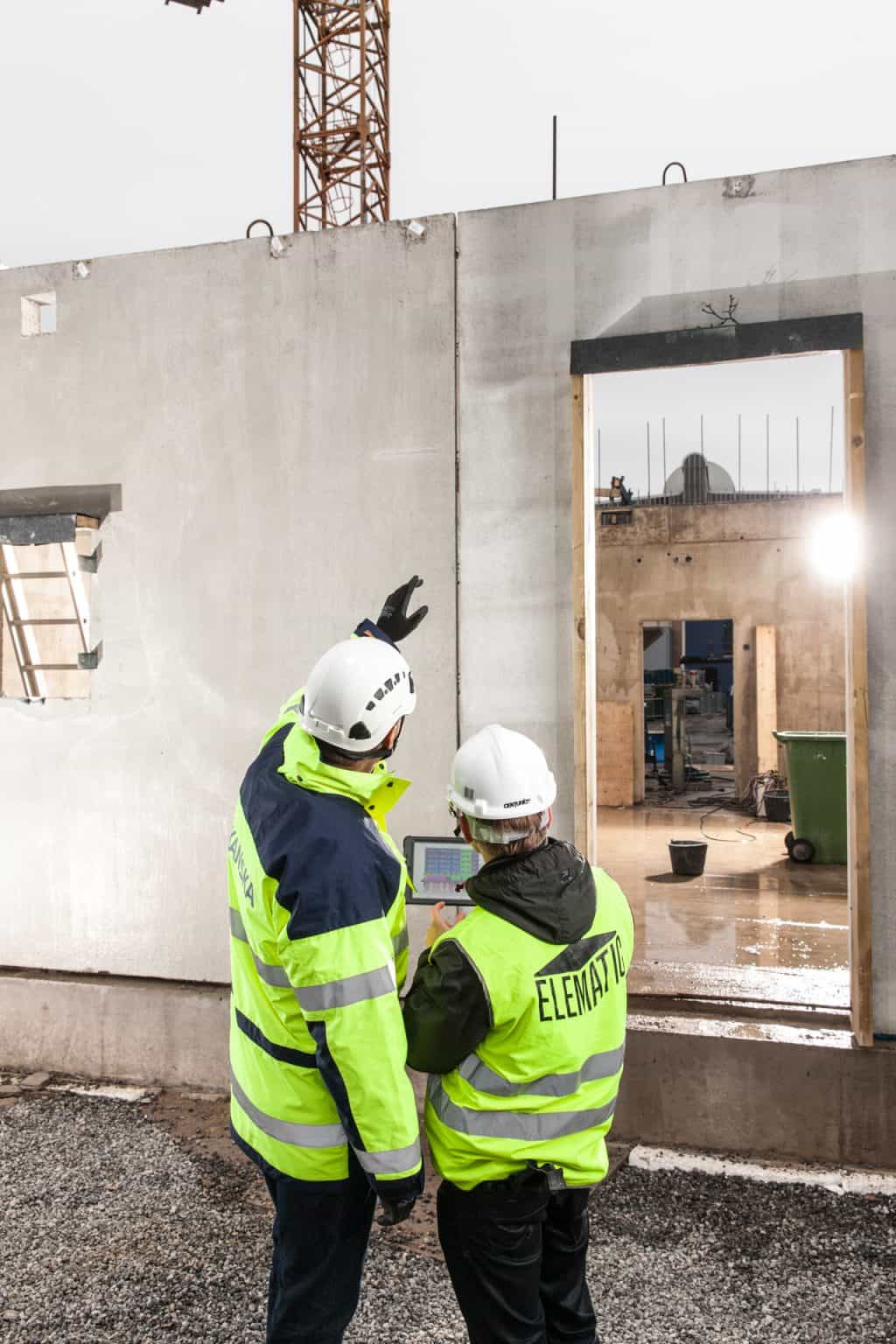
Imagine if workers entering a large construction site would always know where to go, what to do, and where the needed materials and tools are. Workers are proficient in their work, but the reality is that they can add value to the project only in one-third of their work time. The rest of their time is used for locating their tools, materials, and work locations and trying to figure out what they are expected to do.
In today’s digitally connected world, however, there is hope for more efficient construction work on site. A digital situation picture can provide the workers with adequate knowledge about the locations of their work, materials, tools, preceding tasks and current work plan, which decreases confusion and reduces the time needed for material and tool handling, and thus workers can concentrate more on their value-adding work. The digital situation picture improves the productivity of projects also by reducing quality problems due to inadequate knowledge concerning the schedule and right sequences of activities.
A digital situation picture in construction?!
So, what does a digital situation picture mean? It means that information about the past, current and future project activities is available in a digital and interpretable format in real-time. This information is context-specific, meaning that the different roles of a construction project – the owner, designers, contractors, and fabricators – are provided with information that is relevant for them at that particular time, in that location and in that situation.
Current practices to create situational awareness of construction operations are based on many-to-many communication with different methods, coordination meetings, meeting minutes, formal status announcements by partners, and individual observations by workers. It is thus a labour-intensive, manual task that does not produce a good result. Trying to average several incorrect, partial pieces of situational awareness through social processes can never end up with the correct answer.
More systematic and up-to-date situational information would allow project parties to make decisions based on accurate data. As a result, the parties could better plan their future activities.
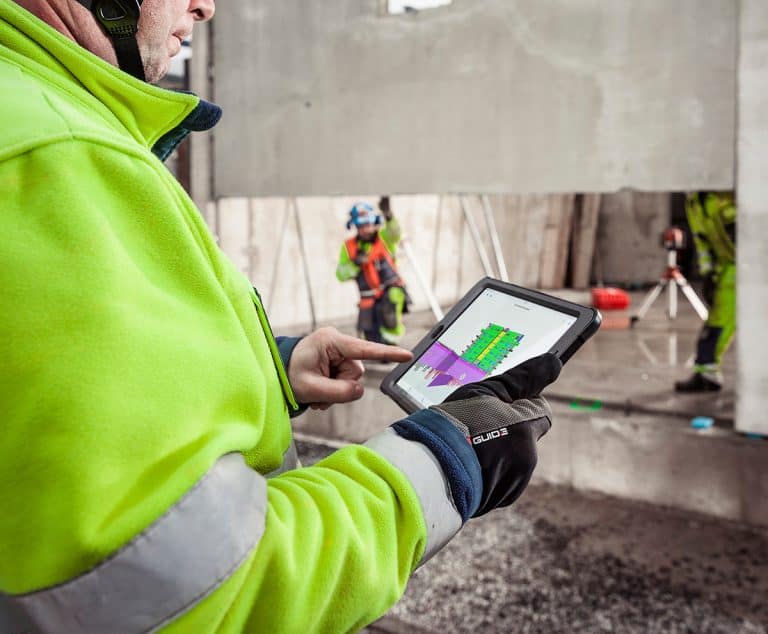
Building the basis for the digital future
The benefits of a digital situation picture could be enormous to the construction sector, but empirical studies on how to form a digital situation picture are scarce. We, as researchers, started to create the necessary infrastructure for a digital situation picture in construction. Our goal is to create a shared data structure (the ontology), and then link data concerning the intended end-product, material logistics, resource movements and supply chain from different sources – BIM (Building information modelling), simulations, ERP systems, IoT sensors, indoor positioning systems, photos, point clouds and onsite communication – to create a real-time situation picture.
We are currently exploring what and how data regarding the creation of a situation picture could be shared between the project parties to allow the creation of a shared situation picture that benefits all project parties through shorter project schedule, better quality, and fewer misunderstandings.
Precast producer’s role in the creation of a digital situation picture
The precast producer plays a crucial role in creating a digital situation picture in construction, which is a prerequisite for the smart supply chain management. For example, the precast producer can positively affect the schedule of a construction project by delivering engineering-to-order products just in time to the site. In practice, as many precast producers have advanced ERP (enterprise resource planning) cloud-based systems in place, the producers can provide real-time information regarding the status – in design, production, delivery – of precast products. This information is critical for the site managers as they plan their production schedule. Of course, to enable just-in-time delivery, the producer needs up-to-date schedule information from the site manager.
The assembly workers on-site, in return, can provide precast producers information concerning the installation of the precast product, for example, whether the product was of good quality and successfully installed. Up-to-date data on the end-products’ quality at the site is an essential input to the quality management process in precast producer’s factories. ‘Installed successfully’ information and other digitally interpretable site plan data can be used by the producer when making decisions on the planning and production schedule of other products for the project, and thus enable more efficient production processes at the factories.
Data during transportation and installation can be collected manually from smartphone apps or use GPS to track transportation. Image data can be used to check the quality and installation location. For example, drones can be used to get accurate point clouds of installations that can be compared to BIM models to detect any issues with tolerances. Similar results can be achieved with crane-mounted cameras, although with lower accuracy.
Data collaboration needed
Sharing data on each party’s activities in construction is new to the sector and necessitates successful examples. No party wants to share business-critical data, but the sharing of the right kind of data can lead to efficiency in operations and win-win situations.
We have identified potential use cases where accurate real-time data can help in the creation of a situation picture. Successful use cases could be BIM-based tendering and contracting, BIM-based bill of materials, and real-time sharing of design and production schedule data, including transportation data. Sensor technology will be a crucial part in providing data on the locations of materials, tools, and site workers for the algorithms that can create information for the decision-making processes of project managers.
The identified use cases necessitate technological, socio-cultural and economic changes in planning and production processes. Smart supply chain management is dynamic and based on common, reliable planning and status data that are shared in real-time by the process stakeholders. Instead of point-to-point data interfaces, open and commonly agreed data structures are obligatory for information exchange to create a digital situation picture in a domain where stakeholders are changing project by project. Data from the supply chain management process should be collected and shared as automatically as possible to avoid time lag or human mistakes. Precast production automation could help by automatically producing interoperable status data for use cases in supply chain management.
Finally, the transfer of data necessitates open interfaces between the parties’ data management systems. So, lots need to happen, and progress might take some time, but the good news is that all these changes are doable. Let’s start implementing bit by bit!
Rita Lavikka, Markku Kiviniemi and Pertti Lahdenperä from VTT Technology Research Centre of Finland and Antti Peltokorpi and Olli Seppänen from Aalto University have researched the topic of building a digital situation picture in construction.
The research is conduction in DiCtion (Digitalizing Construction Workflows) research project, which is funded by Business Finland and six companies operating in the construction sector: Trimble Solutions, Sweco, Ruukki Construction, Fira, Consolis Group/Parma, and Bonava. Trimble Solutions is providing Trimble Connect software that can be used by project parties to share document and BIM data in real-time. Fira is providing an open data platform that integrates end-user applications and IoT data to enable smarter supply chain management.
Writer
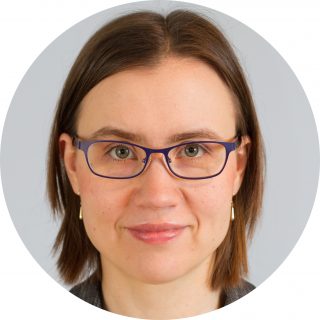
Rita Lavikka
VTT Technology Research Centre of Finland
Writer
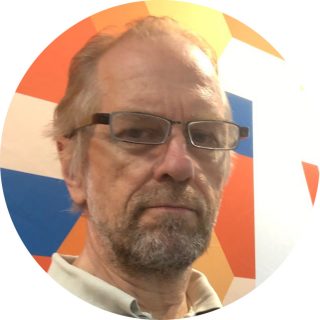
Markku Kiviniemi
VTT Technology Research Centre of Finland
Writer
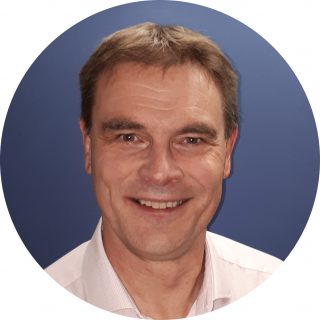
Pertti Lahdenperä
VTT Technology Research Centre of Finland
Writer
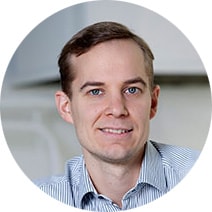
Antti Peltokorpi
Aalto University
Writer
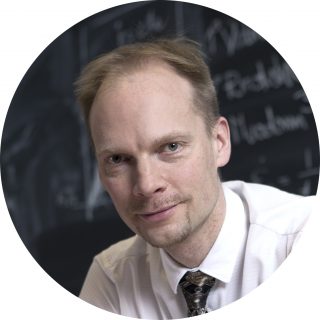
Olli Seppänen
Aalto University