Usability through locally sourced raw materials: Acotec partition wall element
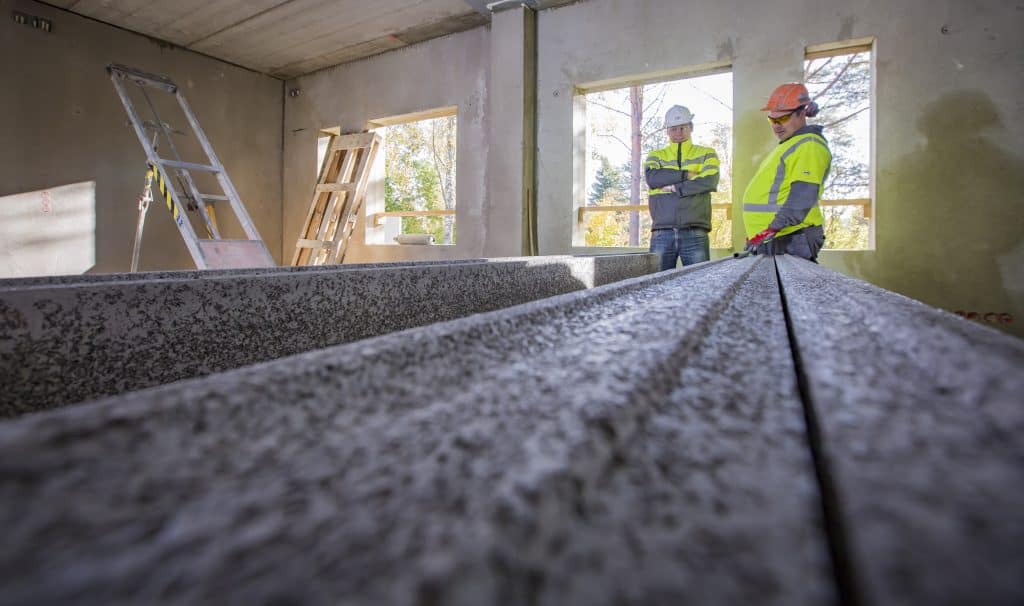
The Acotec partition wall solution is primarily constructed from concrete and lightweight expanded clay aggregate, i.e. Leca – materials, whose availability can be guaranteed all over the world. – The benefits of concrete and LECA include a comprehensive market network, in addition to their other superior qualities, such as moisture resistance, excellent fire resistance and a good sound reduction index. Concrete is available worldwide, and LECA can also be found almost all over the world. Additionally, our customers in China are currently utilising rock-based crushed construction waste on Acotec production line in China. The best possible material for the local requirements and conditions is always determined with the customer before the production of Acotec wall begins, Elematic Product Director Jani Eilola says.
The popularity of materials varies from one continent to another. Concrete is the material of choice almost every time in South-East Asia. – In addition to affordable manufacturing costs, the advantages of concrete include, together with Leca, its great mass that complies with the requirements for sturdy partition walls to improve noise reduction set by construction authorities in many South-East Asian countries, Eilola states.
The surface of the Acotec panel made of concrete is very even, thanks to the production line process, which means that minimal further processing is necessary during the following stage. – Surface smoothness is a significant factor for many customers selecting their material. It generates savings in labour costs, you need very little finishing treatment, Eilola points out.
LECA ensures easy manageability
LECA is used in Acotec manufacturing, especially in Europe and Russia. The slightly higher price of raw material is compensated for with easy installation. – Acotec panels made of LECA can be hoisted into place without any equipment. Additionally, the processing of LECA on site is much easier than the processing of concrete, Eilola continues.
Compared to bricks and blocks, the surface of the Acotec wall made out of LECA is much smoother. – After installation, Acotec surfaces made out of LECA only need to be smoothed over quickly, Eilola goes on.
Our production line enables the use of alternative raw materials
Thanks to the scalability of the Acotec production line, wall panels can also be manufactured by using alternative raw materials. The crushed concrete and bricks used in China with the support from local authorities is a shining example of this. – Over the years, we have strived to find the best recipe for manufacturing Acotec. We want to develop product lines that can produce light, yet durable, end products cost-effectively. We have tested several materials, such as wood fibre and expanded polystyrene beads in our recipes, but found that using a rock-based hollow slab yields the best efficiencies. That is why the Chinese model is a perfect fit for manufacturing Acotec, Eilola says.
Eilola also mentions a Finnish innovation. – There is a method developed in Finland that would replace LECA with beads created as a by-product of the heat treatment used for cleaning contaminated soil. The method is especially suited for areas where there is plenty of land area contaminated by the oil industry, and where rapid urbanisation calls for efficient solutions for construction. The innovation is still being developed, but it shows that when new innovations are introduced, we want to be at the forefront by enabling their utilisation as part of the Acotec panel manufacturing process, he continues.
Installation glue makes or breaks the panel adhesion
During installation, concrete and LECA panels are bound together with a high quality Tilefix joint glue. – The most critical stage of installation takes place when securing the vertical seam: when the concrete dries, the panel shrinks, which may result in cracks. That is why one must use the best quality mortar for the seams, i.e. Tilefix, Eilola says.
The availability of suitable mortars varies between market areas, and that is why Eilola wants to point out that there is always help at hand. In order to improve joint glue quality, Elematic also supports developments. – We have research joint clue widely over the years and have great expertise in the matter, he points out.