Taking benefits of data to next level with IoT
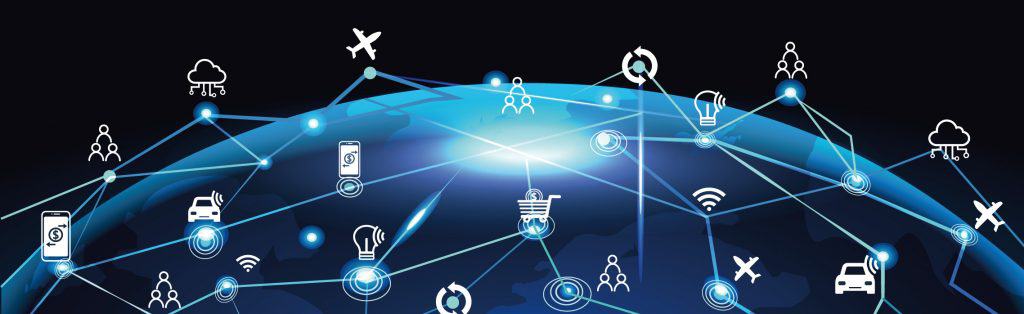
Elematic is developing new Internet of Things (IoT)-based solutions to help the precast industry improve their business through improved use of data.
The construction sector – and the precast industry along with it – has not been the fastest to adopt IoT-based applications. IoT-based apps would allow machines equipped with various sensors to exchange data with other devices over the internet. But that is now changing as more companies are becoming aware of the benefits IoT can bring.
“Whether we talk about IoT, artificial intelligence (AI), or other recent technological trends, it all boils down to data and how companies can use data analytics in their own business,“ says Karan Menon, a postdoctoral researcher at the Tampere University in Finland.
Menon is the project manager of SNOBI, a Business Finland-funded project that helps manufacturing companies transform their business models to advanced data-driven ones. As one of the participants in the project, Elematic is focused on developing IoT solutions for the precast industry’s needs and requirements.
“Data from machines can help you optimize their continuous use in real-time, making work easier and more sophisticated at the same time. However, you should not adopt IoT just for the sake of it. Each company should evaluate and decide which solutions and features can bring the most value to their operation and business,“ he says.
Foundations for new solutions already exist
In precast production, new Elematic machines and software solutions already offer a wide range of intelligent features. Plant Control, for example, is an Enterprise Resource Planning (ERP) solution specifically designed for precast factories. It provides a digital data-based system for optimizing the production process and includes manufacturing execution systems for both floor (FloorMES) and wall (WallMES) production.
“With these solutions, we can gather and store various data from the machines during different stages in the production process. Having access to real-time information about the situation in the production line enables you to react at an early stage if the work is behind schedule,“ says Jani Eilola, Product Director, Floor technologies and Acotec.
“Storing information about the prestressing of individual hollow core slabs into the factory’s quality database is also now possible. The next step is to get the most out of this data by developing IoT-based services.“
With IoT solutions, detailed telemetry data, such as a machine’s screw wear, collected from various sources and locations can be transformed into insights through analysis and by combining it with information from other systems, such as the company’s ERP and CRM software. This provides many opportunities.
”One way to look at this is to think of data as means of getting into the objective root causes of an issue, whether it’s related to optimizing production and material use or fixing quality issues,” suggests Toni Koitmaa, Product Director, Wall Technologies.
“Imagine, for example, if we had data about the exact amount of mold oil used when manufacturing each element. If a quality issue in the façade of a finished wall element arises, we can pinpoint if it is due to excessive use of mold oil, as we have the data to provide answers,“ Koitmaa posits.
Data analysis would also support service and maintenance processes currently in place. Could machine breakdowns during production be prevented, for example, if signs of wear and tear are monitored automatically in real-time, allowing spare parts to be ordered early enough and when they are available in stock?
“When it comes to IoT, we should focus on solutions that can deliver cost savings and boost productivity through, for example, improved predictability and learning,” Leena Raukola, Customer Service Director at Elematic, points out.
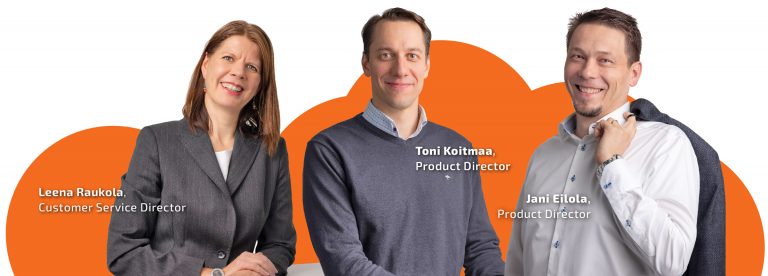
Turning ideas into reality
The possibilities offered by improved use of data are promising and exciting. At Elematic, the drive is on ways to use these possibilities to improve existing services to customers.
“Developing IoT-based solutions for improved use of data is something we want to do in close cooperation with the future users of these services – people at the factories. We want to learn what services and data would benefit them most and how we can better develop our machines based on user experience. This is why input from factories are truly valuable and appreciated,” Eilola concludes.
“Each company should evaluate and decide which solutions and features can bring the most value to their operation and business.”
Internet of Things explained
- Internet of Things (IoT) is made up of devices – from sensors to smartphones – connected to and exchanging data with one another over the internet.
- IoT is enabled by the development of sensors, software and other technologies, such as real-time analytics, machine learning and automation.
- Industrial Internet of Things (IIoT) refers to the use of IoT in industrial sectors and applications, such as in manufacturing and supply chain management.
- The advantages of IoT for businesses include reduced costs and emissions, improved productivity and efficiency, better customer services and experience, and improved work safety, among others.
ORDER OUR NEWSLETTER OR CONTACT US
or