Extruder according to production capacity
“Elematic’s flagship E9 is the first extruder in the world with 100 percent shear compaction automation, incorporating remote monitoring,” says Elematic’s Product Director at Elematic, Jani Eilola, explains. Extruder The E9 extruder is a highly automated, robust machine for continuous production of slabs up to 500 millimetres millimeters in height. The E9 does not require an operator to oversee the production.
The extruder S5 extruder enables represents a lower-cost investment for new entering entrants to the market with a smaller production capacity. It was released in at the beginning of 2014. The little sister of E9 incorporates the same shear compaction technology with less automation. The lighter S5 is a lighter extruder that can produce slabs up to a height of 320 millimetres.
Easy serviceability
The serviceability features of the E9 and S5 bring savings to the customer. Developing the extruders’ maintainability has cut the number of hours of spent replacing the screws and bearings in half, for example. “Both extruders have a modular structure, allowing the use of several nozzles with the same power unit. Changing the nozzle for to producing produce different end product types is easy: locating most technology in the power unit makes the nozzle affordable, and quick to replace,” Eilola says.
“With the latest technology, a very low level of strand slippage can be achieved. A new strand guide was developed to hold the strands in a right place,” Eilola explains.
“To predict production performance, the ability to plan service is vital. With shear compaction technology, maintenance of the machinery can be carried out as planned,” Eilola says. A reliable fleet equals reliable precast production and delivery – on time, every time.
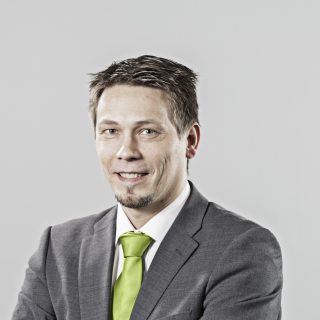
Jani Eilola