At your service – Live and remotely
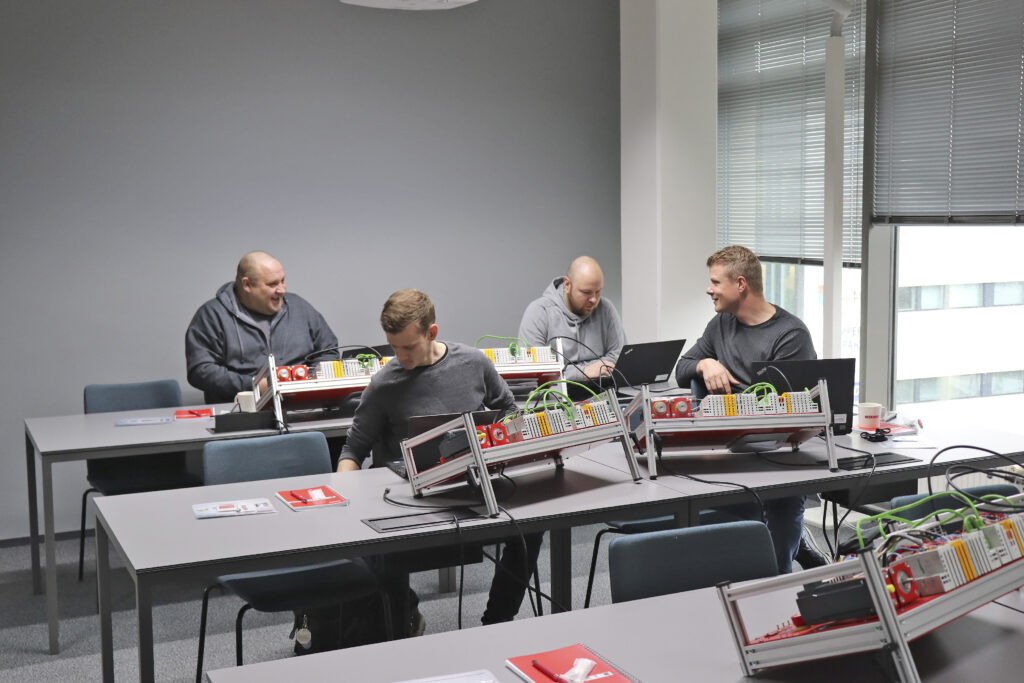
At the heart of Elematic’s lifetime commitment promise, you will find the members of the service team. Their job is to make sure that the production of precast panels in factories all over the world can go on without unnecessary interruptions.
While the coronavirus might have challenged them and at times slowed them down, it takes more than a pandemic to stop the service team!
Is it possible to know all Elematic machines?
The service team consists of Customer Service Director Leena Raukola, Customer Support Manager Eija Aimolahti, Service Manager Pia Viitanen and ten permanent service engineers: eight in Finland and two in Dubai. In addition, Elematic has service engineers in India and the US and from time-to-time external personnel is also called in for customer support and installation supervision.
Customer Service Director Leena Raukola has been with Elematic for 22 years in many different positions. “Especially my many years in charge of product development are very useful, because I know our machinery quite deeply, which is good when supporting my team,” she explains.
With her 30-year-long history with Elematic, Eija Aimolahti also knows the backlist of equipment well.
“Our machinery is very long-lasting, so our customers still have machinery, for example from the 90s, and I’m familiar with it,” Aimolahti says.
“The very best thing about my work is when I can help customers straight away. Perhaps they have a big problem, and the production has stopped, and then it feels amazing to be able to send the best people out to them. Our service engineers are so good! I can really rely on those guys,” she adds.
Service Manager Pia Viitanen is a new reinforcement.
She joined the service team in November 2021, and she says that she has been warmly welcomed and has not encountered any real problems. “One big matter is how I can get to know all the machinery that Elematic has manufactured during the decades,” Viitanen notes.
“It’s sometimes hard to allow myself to not know as much as Eija. Fortunately, we have excellent service engineers!”
Uncertainty gives frustration
A working day in the service team has never been boring, but when the coronavirus swept over the world, the team’s work became even less predictable than before.
“For weeks and months, we have started the same work every morning. We have scheduled visits and planned installation supervisions and such – and new restrictions and lockdowns have come in the way,” describes Raukola.
The uncertainty brought by the pandemic has been extremely frustrating for Raukola’s team as well as for precasters in need of support. Everybody has had to stretch a little extra to provide the best service possible.
“What is helping us is that we have long relationships with many of our customers. We know each other, which makes it much easier to discuss and replan visits and machinery start-ups,” Raukola notes while thanking the customers for their cooperation during the pandemic.
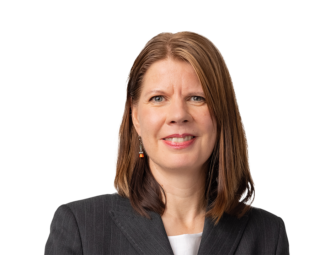
Leena Raukola, Customer Service Director
Automation and virtual reality
Remote service is not a new phenomenon at Elematic.
With a helpdesk launched already in 2004, the company was one of the first in the business to offer precast support remotely. The service team can also connect remotely to any newer machinery, which makes remote service straightforward.
To improve the remote services further, the team has tested modern technology, such as virtual reality glasses. The technology is both promising and challenging, as the equipment is expensive, and the software needs to be more developed. Limited wi-fi connections at precast plants can also bring problems.
“Though we’ve faced a lot of challenges with the VR glasses, I believe that the conditions will improve in the future. This is the way we are going,” says Raukola.
Remote training has come to stay
It comes as no surprise that the demand for remote training has increased during the past years.
Elematic offers different webinars and training online, related to machines, productions processes, and safety. Online courses can be customized to each factory’s specific needs.
Raukola, Aimolahti and Viitanen all agree that more training, as well as service, will happen remotely, even in a post corona world.
“The pandemic has opened new ways to work. Remote sessions are a cost-efficient way to train the workers.
I strongly believe this is the new normal,” says Viitanen.
A general lack of skilled labor also raises demand for remote training. As precast machinery gets more automated, operating it requires a higher level of knowledge, adds Aimolahti.
“A future trend in my work is that remote support and training, such as webinars, will be more common,” she notes. “This is part of a development that allows us to offer support in a more efficient, fast, and environmentally friendly way.”
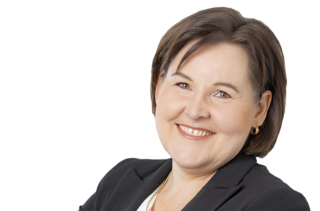
Pia Viitanen, Service Manager
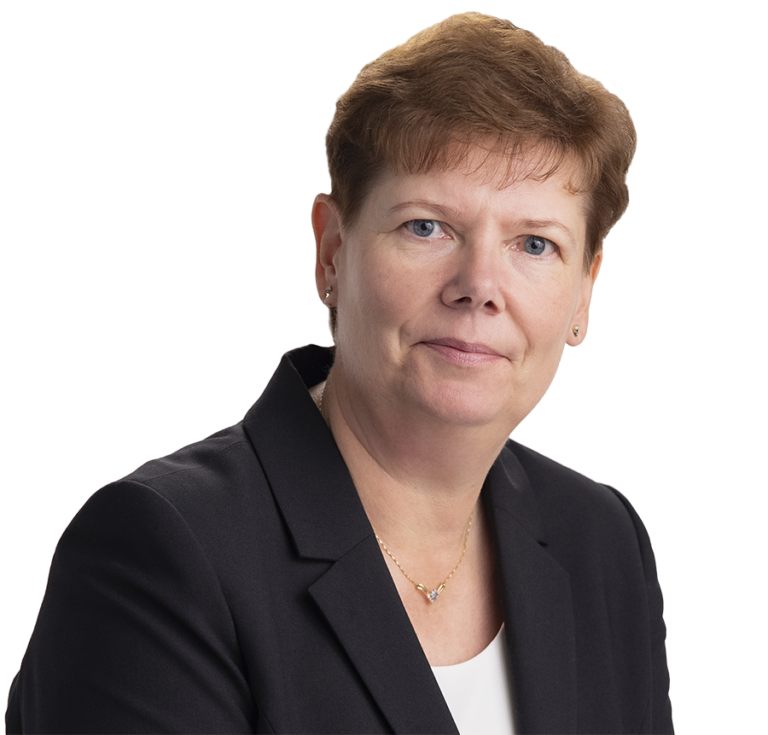
Our machinery is very long-lasting, so our customers still have machinery, for example from the 90s, and I’m familiar with it.