Rethinking solar foundations: Elematic’s industrialized model for precast hollow core piles
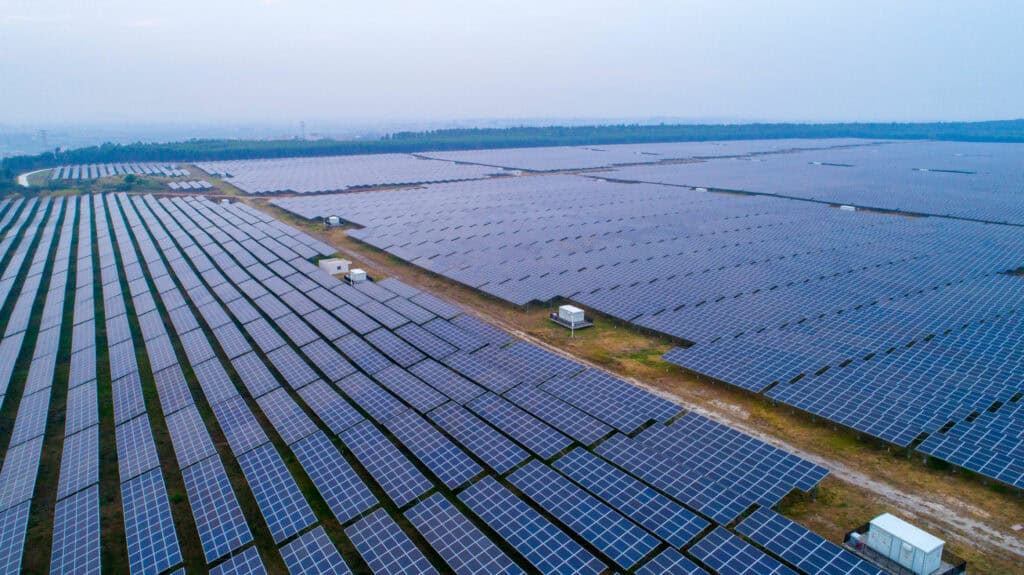
Solar energy is scaling faster than ever. What began with small rooftop systems has now grown into gigawatt-scale solar farms, built at a pace once unimaginable. As projects grow exponentially larger, every component’s efficiency becomes more critical. While panel technology and power electronics have made great strides, foundation solutions lag.
Steel piles, though cost-efficient and rapid to install, struggle with corrosion and a low load-bearing capacity when presented with challenging ground conditions. Concrete piles, though durable, face their own challenges:
- Cast-in-place concrete piles are labor-intensive and slow to produce at scale.
- Solid precast piles consume excess material and are often produced with suboptimal factory processes.
- Spun piles, which are centrifugally cast, require a slow batch process requiring costly specialized molds and large factory space, making them extremely capital-intensive at scale.
At Elematic, we believe solar projects deserve a foundation solution built for the scale and speed of today’s industry. That’s why we’ve developed a truly industrialized model for precast piles. A system that eliminates the inefficiencies of traditional concrete pile solutions and redefines how solar foundations are designed, manufactured, and installed.
Starting with the right pile
A one-size-fits-all approach doesn’t work for solar farm foundations. Soil conditions, climate, and regulatory requirements vary from site to site, making it essential to use a pile tailored to the project’s environment.
That’s why at Elematic, in collaboration with Sweco, we begin every project with a technical assessment and optimized pile design, ensuring maximum structural efficiency, material savings, and long-term performance.
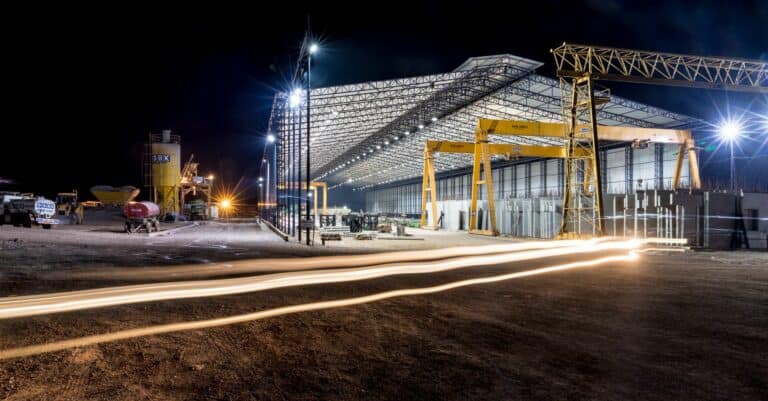
Key benefits of Elematic’s piles:
- Material-optimized designs reduce concrete use by up to 35%.
- Pre-stressing of concrete provides crack resistance and a higher load-bearing capacity.
- Hollow core designs can accommodate an internal height-adjusting mechanism, allowing panels to adapt to sand or snow accumulation.
- Factory-controlled production with world leading Elematic Extrusion system ensures that every pile meets strict quality parameters, eliminating inconsistencies found in on-site methods.
A streamlined factory designed for flexibility
But a great pile is only part of the equation. How it’s made and where it’s made matters just as much.
Unlike traditional and costly fixed-location precast plants, Elematic’s modular factory can be set up on-site or in a regional hub. After project completion, the production equipment can be relocated or repurposed, maximizing long-term investment value
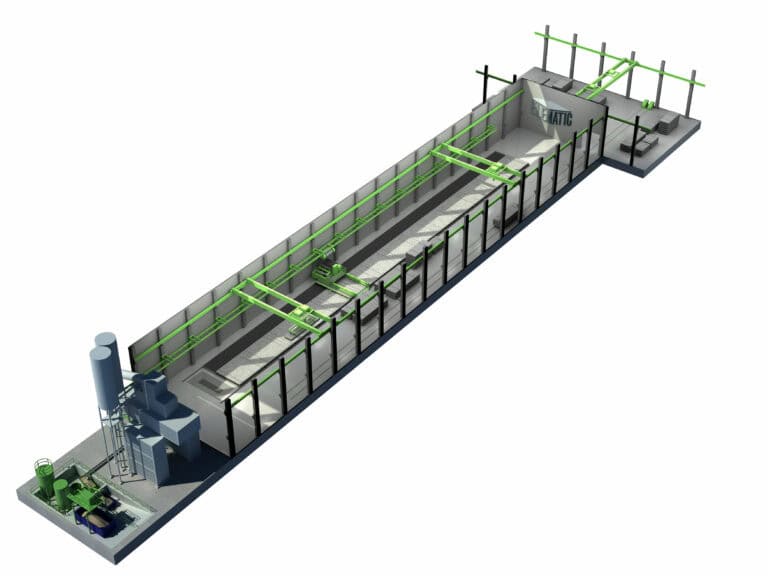
Key features of Elematic’s precast factory:
- The factory can be set up near the project site(s), reducing logistics costs.
- Requires only 4,400 m² layout to produces up to 4.4km of piling per day
- Requires only 10-15 workers to operate, significantly reducing labor costs
Automated production process for maximum output
At the heart of our factory is a continuous, long-line extrusion process that allows us to cast multiple piles in one seamless operation.
Compared to traditional batch-based precast systems, Elematic’s continuous casting process significantly reduces handling, time, and labor, while increasing output. This directly translates to higher efficiency, lower costs, and faster project completion.
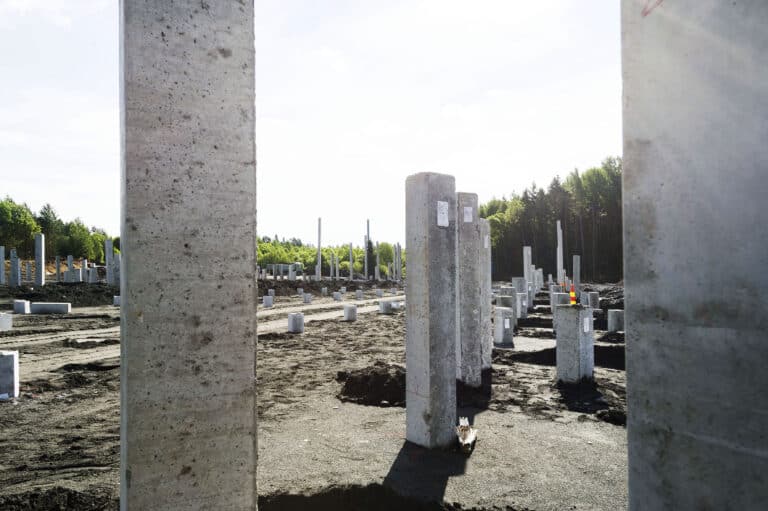
Key advantages of production process
- Automated process with 8x150m casting beds allow for 50% higher output than traditional batch precast methods.
- <1 percent material waste, with automated quality & safety control.
- Controlled factory-environment ensures consistent pile specifications, eliminating variability of on-site casting
This level of production efficiency directly translates to lower costs, shorter lead times, and faster project schedules.
Digitalized pile installation
roducing a great pile quickly is one thing but getting it into the ground just as efficiently is just as critical. That’s where digitally guided installation comes in.
Instead of relying on manual labor and guesswork, our piling system uses digital control to ensure millimeter-accurate placement. We utilize Machine guidance system to ensure Pile alignment via satellite positioning.
This reduces errors, minimizes rework, and accelerates installation—getting solar farms up and running faster than ever.
Installation process highlights
- Up to 600 piles can be installed per day, cutting the foundation work time in half.
- Digital control ensures millimeter-accurate placement, reducing errors and rework
- Machine-led process requires only a small crew, lowering reliance on skilled manual labor.
Reduced installation times allow solar projects to start generating power, and revenues, sooner.
A holistic approach to solar foundations
We’re not just improving one part of the process; we’re rethinking the entire foundation system to make it faster, smarter, and more scalable.
Why choose Elematic’s solar pile solution?
- A highly optimized pile design that reduces material use and offers height-adjustability.
- A modular, relocatable precast factory that maximizes production efficiency with minimal workforce.
- A fully automated production process for high quantity & high-quality output.
- A digitally controlled installation system that minimizes deployment time.
With faster foundations, solar projects reach energy production sooner, unlocking revenue faster. If you are a developer looking to scale up your solar projects while avoiding the bottlenecks of conventional foundation methods, contact our team today.