Amazing project, amazing people
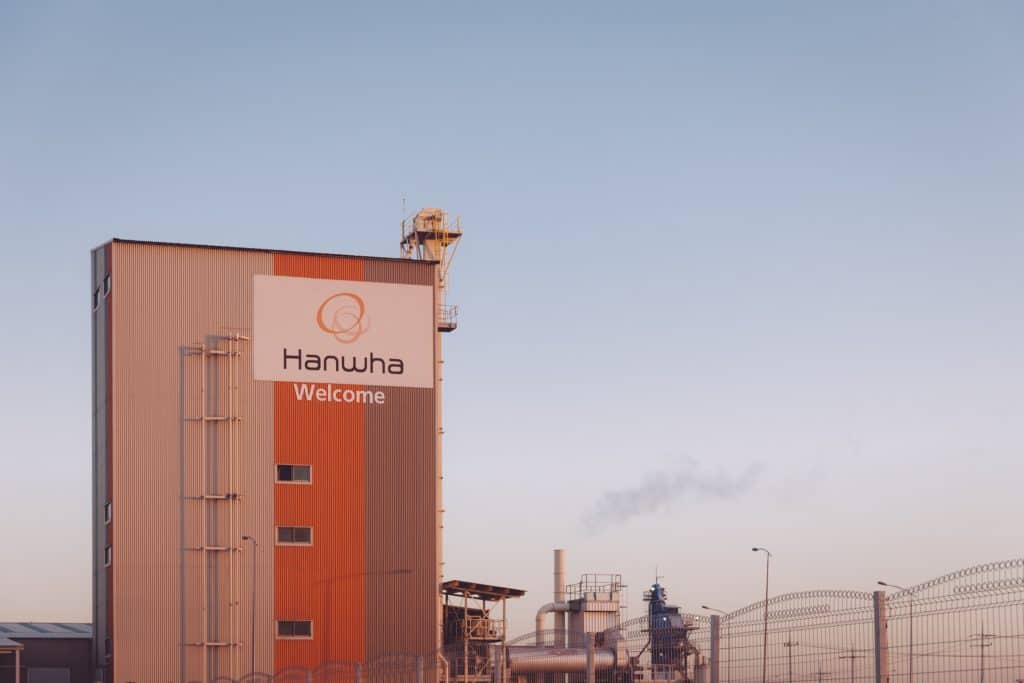
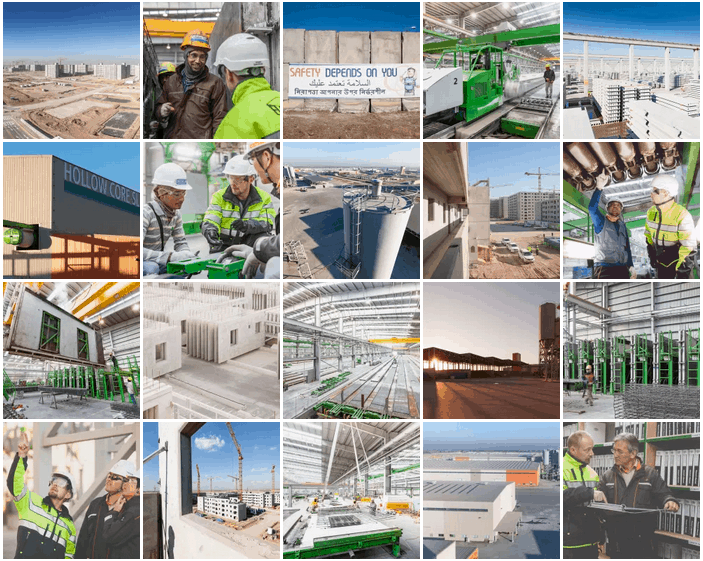
In January 2014, when I arrived to Bismayah first time, the site was really busy: equipment installation was going on with full speed. You could hear a dozen languages spoken at the same time as subcontractors from all over the world were keenly working on their machinery. Before my arrival I had obviously seen photos of the site but still was truly impressed by the actual size of the area and by the huge number of people working there to make it all happen.
At that time, a big part of Elematic equipment had already arrived at the job site and some were even installed and ready to rock and roll, what comes to the mechanic side of things. However, there were some bits and pieces – mainly molds and shuttering – still travelling on the sea and arriving later that spring.
The installation team had finished the mechanics of the batching and mixing plant at the sandwich wall factory and also the first circulation line was completed. The electricians were just working on those two. My first task was to test the electrics in the two plants, so during the first few weeks of my stay I spent my days mainly doing just that: testing and also adjusting the programming. There was no time to waste as we had to get the production running so as soon as I had completed all finalizing work, I started to train the operators. Everything was new to them and in the beginning there were a lot of questions in the air. As usual, the biggest challenge was the language barrier but I am used to it as quite often we need to do the training with interpreters. So we found a way to communicate and, in the end, everyone was satisfied with the outcome
But there were more equipment to install and adjust so on I went. The next task was to ”tune” the batching and mixing plant and the concrete transportation for the hollow-core factory, at the same time as the production was already starting. The work continued with starting the batching and mixing plant for the battery mold factory as well as concrete transportation and the casting machine.
The final task was to finish the two circulation lines. When the summer arrived, every factory was in operation. For me this meant that there was a huge not only a flow but a flood of questions coming from here and there, as the operators and service guys did not have much experience of using the equipment at that stage. It’s understandable and perfectly normal, only this time the delivery was of such a gigantic size that this took a big bite of my working time. Of course, this changed when time passed and people learned.
At the end of the summer, we were taking into use the last machines, the modifiers at the hollow-core factory. This was actually quite an extensive task as we needed to transfer all slab information to the plotters and go through all drawings manually, in order to make sure that the shuttering was correctly programmed into the database.
When everything was in place and in operation, we started timing the lines, each one individually, to ensure that the production rate was as planned. This meant some adjustment work – for example we optimized the parameters at the batching and mixing station so that the preset speed and accuracy were reached. The concrete transportation system also needed some attention; we tuned it and removed all unnecessary delays. Finally we were ready for the final inspection from the customer, Hanwha E&C, side – they checked and approved the delivery one line at a time. At that time both of us, Hanwha people and Elematic , were pleased as the work of both of the team was accepted altogether and the production team could take over fully working factories. We also agreed that I would go back to take care of some warranty jobs and changes – which I did, in February 2015. But this was not my last time at Bismayah as in the autumn of the same year we took into use two extruders, a saw and a modifier that the customer had bought after the main delivery.
It was quite a challenge at first to work at such a big site where the only common language was English, obviously. However, the level of language skills varied a lot, and sometimes it was quite difficult to find out what the other one actually meant. A funny thing was the relationship with one of the guys operating the machines: he couldn’t speak a single word of English so whenever he had any questions or problems, he just came to me and waited in silence until I noticed him. Then we went together to his machine and he showed me the point that he found problematic, without ever saying a word. But we managed to find a solution every time. And, as time went by things got easier with this operator as well as with other people when we learnt to know each other. Then it was easier to understand what we meant, even if we still didn’t understand each and every word that we said. Sometimes also cultural differences in handling the business caused some funny surprises to both parties – but all was solved in the end.
I am grateful and proud of having had a chance to be a part of such a big, unique project – and, above all, happy about all my new friends and buddies with whom to go fishing!
Writer
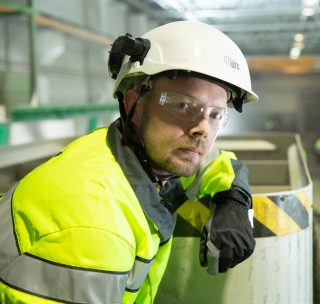
Janne Elomäki
Customer Support Engineer
Elematic